Технология автоматического превентивного обслуживания промышленного оборудования
VibroBox — это сервис предписывающего обслуживания (Prescriptive Maintenance, RxM) для промышленного оборудования. Основан VibroBox на непрерывном анализе технического состояния оборудования посредством объединения вибрационных сигналов и данных телеметрии, постоянно поступающих от оборудования, с его виртуальной параметрической моделью (называемой также «цифровой двойник»). Применение VibroBox существенно оптимизирует многие бизнес-процессы как крупных, так и небольших предприятий.
VibroBox даёт клиентам исчерпывающую информацию о техническом состоянии их оборудования и предписания по его эксплуатации и техническому обслуживанию. Она доступна в личном кабинете пользователя с любого подключенного к интернету устройства.
Наилучшие результаты достигаются путём интеграции VibroBox с системами управления производственными активами (CMMS, MES, ERP). Самый эффективный путь к этой интеграции — посредством глобальных платформ для промышленного интернета вещей (IIoT) и Индустрии 4.0. Крупнейшими из них являются Predix, SAP Cloud Platform for the Internet of Things и Intel IoT Platform. Основная цель VibroBox — стать ключевым сервисом RxM.
VibroBox работает как облачный сервис, использующий собственные базисные функции, вейвлетный анализ и другие алгоритмы цифровой обработки сигналов (ЦОС), машинное обучение на основе нейронных сетей (Machine Learning, ML) и алгоритмы нечёткой логики (Fuzzy Logic). Именно в этих областях сосредоточены основные компетенции нашей команды учëных, инженеров и экспертов под руководством кандидата технических наук Игоря Давыдова, который уже более 15 лет занимается промышленной вибродиагностикой и ЦОС.
VibroBox испытан на двигателях, прокатных станах, компрессорах, ветрогенераторах и другом оборудовании предприятий Беларуси, России и Китая.
Ключевые преимущества VibroBox:
- диагностика и управление техническим обслуживанием оборудования полностью автоматические. Все алгоритмы функционируют в «облаке» и не требуют участия людей-экспертов;
- сервис оперирует текущим состоянием оборудования, его режимами и технологическими рисками на уровне конкретных деталей (износ наружного кольца подшипника или шестерни, бой вала, раковины на телах качения и т.д.);
- сервис легко масштабируется;
- применение математического моделирования, при котором «цифровой двойник» оборудования параметризуется реальными данными телеметрии;
- работа с практически любым роторным и поршневым оборудованием без необходимости длительного предварительного «обучения» сервиса;
- работа с широким спектром промышленных датчиков и других источников данных телеметрии;
- возможность эффективной интеграции с автоматизированными системами управления активами.
Команда VibroBox также работает над уникальными алгоритмами выделения признаков анализируемых сигналов различной природы (например, акустическими, эхо-шумами сердца, ЭКГ, ЭЭГ, звуками речи и т.д.). Эти алгоритмы в будущем помогут создать универсальный облачный классификатор сигналов, а также существенно увеличить эффективность существующих фреймворков искусственного интеллекта (Artificial Intelligence) вроде Google Cloud Machine Learning Services или Microsoft Azure Batch AI Training.
Далее более подробно описываются структура сервиса VibroBox, его датчики, алгоритмы обработки вибрационных сигналов, а также перспективы в рамках IIoT и Индустрии 4.0.
Содержание
1. Для чего нужно предписывающее обслуживание?
2.1. Современная практика технического менеджмента промышленных активов
2.2. Место диагностики в рамках IIoT и Индустрии 4.0
2.3. Что мешает современной диагностике стать частью Индустрии 4.0?
2.4. Что делает наш сервис уникальным?
5. Аппаратная платформа сервиса VibroBox
5.2. Датчики для съёма вибрационного сигнала и данных телеметрии
5.3. Блок связи и передачи данных телеметрии
5.4. ICP (IEPE)-конвертеры VibroBox
5.5. Блок съёма данных телеметрии для монтажа на DIN рейку
6. Система обработки информации сервиса VibroBox
6.1. Вибрационный сигнал и данные телеметрии
6.2. Блок автоматического анализа кинематической схемы оборудования
6.3. Блок уточнения скоростей вращения роторных компонентов оборудования по вибрационным сигналам
6.4. Набор алгоритмов для вычисления метрик (ISO, ГОСТ, пик-фактор, коэффициент эксцесса и т.д.)
6.5. Набор алгоритмов для оценки спектра сигнала и спектра огибающей вибрационного сигнала
6.6. Набор алгоритмов для вейвлетной обработки вибрационного сигнала
6.7. Базисная вейвлет-функция, адаптированная для выделения ударных импульсных процессов
6.8. Вектор информативных признаков технического состояния оборудования
6.9. Классификация дефектов в пространстве информативных признаков
6.10. Формирование предписаний по эксплуатации и обслуживанию оборудования
6.11. Результаты работы сервиса VibroBox
1. Для чего нужно предписывающее обслуживание?
![]() |
Своевременно не выявленные проблемы оборудования (такие, как отсутствующая либо загрязнённая смазка, превышение допустимой нагрузки на механизмы) способствуют появлению и ускоренному развитию дефектов. Это приводит к внезапным поломкам, крупным потерям времени, а зачастую и катастрофам. Правильная и своевременная реакция на проблему существенно увеличивает надёжность и безопасность оборудования, тем самым сокращая риски и капитальные вложения в бизнес. |
Предписывающее обслуживание (Prescriptive Maintenance, RxM) — концепция, позволяющая эффективно управлять производственным оборудованием путем выдачи предписаний об их функционировании и обслуживании.
![]() |
RxM позволит уйти от внеплановых ремонтов внезапно отказавшего оборудования и увеличить межремонтные интервалы. Также в прошлом останутся аварийные ситуации и катастрофы, связанные с недопустимым износом оборудования. |
Современные системы управления эксплуатацией и обслуживанием основаны либо на мониторинге простых метрик (CBM), либо на экспертно-ориентированных технологиях прогнозного (PdM) и предписывающего (RxM) обслуживания.
Системы CBM используются в основном для аварийной остановки оборудования в связи с выходом за допустимые границы интегральных параметров его работы (температуры, общего уровня вибрации, потребления тока и т.д.). Технология PdM более эффективна, но не позволяет предотвратить поломку, поскольку работает с уже развивающимися дефектами (хоть и на ранней стадии их развития).
Экспертно-ориентированные технологии RxM являются чрезвычайно дорогим, не масштабируемым и ненадёжным решением, поскольку требуют постоянных обучения и поддержки технически оснащённой команды экспертов.
Предпринимаются попытки создания эксперт-независимых систем PdM и RxM на основе объединения мониторинга простых метрик (Condition Monitoring) и машинного обучения. Такие системы требуют чрезвычайно длительного периода обучения нейронных сетей (месяцы, и даже годы) и повторного обучения даже при изменении режимов работы оборудования или после его ремонта. Также они не позволяют эффективно контролировать техническое обслуживание, поскольку не работают с конкретными дефектами внутренних компонентов оборудования.
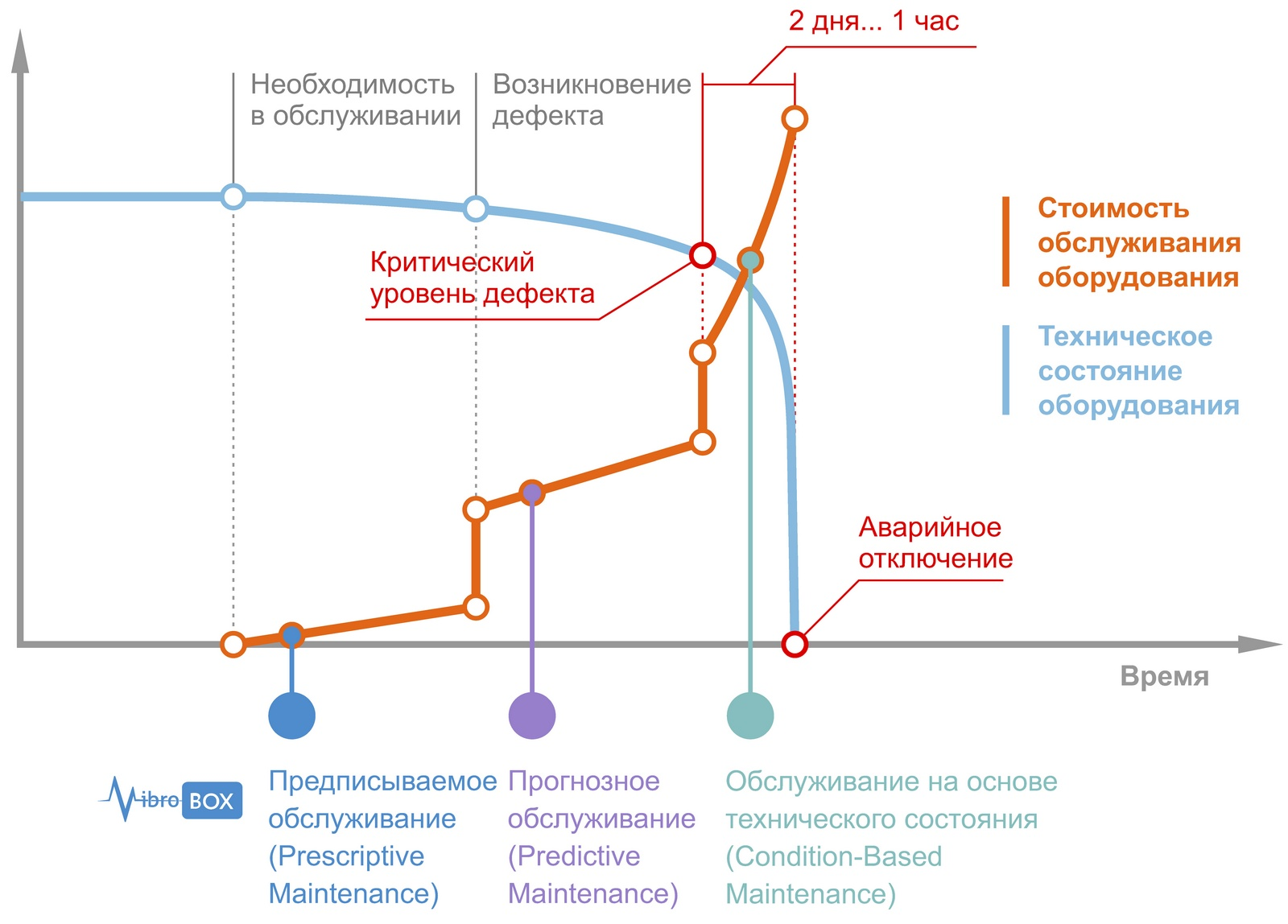
С VibroBox вы получаете автоматический и хорошо масштабируемый сервис RxM, дающий предписания по техническому обслуживанию оборудования тогда, когда это необходимо для предотвращения появления дефектов.
2. Почему появился VibroBox?
2.1. Современная практика технического менеджмента промышленных активов
Невозможно эффективно управлять производственными процессами без знания актуальной информации об их техническом состоянии и режимах работы конкретных узлов оборудования. Существует два практических подхода к оценке технического состояния промышленного оборудования, которые иногда совмещаются либо применяются по отдельности: мониторинг и диагностика.
Мониторинг технического состояния предполагает непрерывное отслеживание ряда параметров промышленного оборудования (температуры узлов, общего уровня вибрации, пик-фактора и т.д.) и реагирование системы (или оператора) на выход этих параметров за допустимые пределы. Реакция может включать в себя остановку технологического процесса, проведение детальной диагностики проблемного оборудования, останов оборудования на ремонт.
Диагностика промышленного оборудования — это комплекс мероприятий, предполагающих углубленный анализ состояния оборудования, его составных частей и режимов их функционирования. Цель этого анализа — выявление дефектов и формирование предписаний по эксплуатации и обслуживанию оборудования.
В зависимости от степени участия экспертов в оценке технического состояния оборудования, различают экспертно-ориентированные и автоматизированные системы.
Экспертно-ориентированный мониторинг и диагностика промышленного оборудования
На предприятии работает коллектив экспертов, оснащённый средствами съёма и анализа вибрационного сигнала — отдел мониторинга и вибродиагностики. С помощью специальных приборов они фиксируют вибрацию оборудования, записывают и обрабатывают её. Далее, анализируя параметры этих сигналов (чаще всего спектральными методами), они пытаются оценить техническое состояние оборудования и определить дефекты конкретных узлов.
Автоматизированные системы мониторинга и диагностики
Будущее систем оценки технического состояния оборудования — полностью автоматические решения, и производители систем диагностики делают шаги в этом направлении. Существует ряд систем вибродиагностики (чаще всего стационарных), которые способны автоматически диагностировать конкретный экземпляр оборудования в конкретных режимах его работы. Внедрение такой системы подразумевает проведение длительного этапа научно-исследовательской работы всё тем же коллективом экспертов, сформированным на базе отдела диагностики либо на условиях аутсорсинга. Они строят математическую модель оборудования, собирают информативные признаки и создают специализированное программное обеспечение. В результате это ПО способно диагностировать конкретную единицу промышленного оборудования при конкретных условиях эксплуатации. Это является не столько решением, сколько попыткой обучить системы диагностики, проецируя на нее ограниченный опыт команды экспертов.
Решать задачи вибрационной диагностики таким способом чрезвычайно затратно и организационно, и финансово. Обучение, мотивация персонала, контроль его работы и преемственность опыта, закупка дорогостоящего вибродиагностического оборудования — это лишь часть проблемы. Такое решение не масштабируется, вынуждая предприятие повторять все пройденные ранее этапы внедрения при изменении производственных процессов. Затраты на организацию и поддержку вибродиагностики становятся неоправданно велики.
Итак, основные проблемы современной вибродиагностики:
- высокий порог вхождения — как организационный, так и финансовый;
- дорогостоящие обучение, мотивация, контроль и низкая преемственность опыта команды экспертов;
- дорогостоящие приобретение и поддержка средств вибродиагностики;
- технические и организационные препятствия на пути масштабирования систем.
VibroBox решает задачу автоматизации RxM для промышленного оборудования на качественно новом уровне. Достигается это без создания узкоспециализированных стационарных систем и без проведения предварительной исследовательской работы коллективом экспертов «на местах». Это фактически делает VibroBox легко масштабируемым сервисом, который автоматически обучается на снимаемых каждый день массивах данных, снимаемых с широчайшего спектра подключенного к сервису оборудования.
2.2. Место диагностики в рамках IIoT и Индустрии 4.0
Индустрия 4.0 (Industry 4.0) — инициатива массового внедрения киберфизических систем в производственные процессы и системы управления предприятиями. По мнению инициаторов это должно привести промышленность к четвертой индустриальной революции.
Инициатива Индустрия 4.0 была выдвинута в 2010 году правительством Германии и впоследствии получила поддержку стран Евросоюза. США в 2014 году последовали примеру и создали некоммерческий консорциум Industrial Internet of Things (IIoT), которым руководят лидеры промышленности — такие как General Electric, AT&T, IBM и Intel.
Системам диагностики в рамках этих концепций отведена важная роль. Оборудование должно за счёт встроенных систем полностью автоматической диагностики уметь оценивать своё техническое состояние и сообщать о проблемах в систему управления активами предприятия. Выявление рисков, дефектов оборудования (вплоть до его конкретных узлов), оценка остаточного ресурса, формирование предписаний по эксплуатации и техническому обслуживанию — всё это должно осуществляться без участия людей.
![]() |
Автоматизированные системы управления предприятий (CMMS, MES, ERP), получая входные данные от систем RxM, реагируют на выявленные риски соответствующим образом. Они корректируют режимы технологических процессов, проверяют наличие на складе необходимых комплектующих, заказывают их в случае необходимости. Находят окна в технологическом процессе и формируют заявки на точечное и своевременное обслуживание. Всё это обходится без длительной остановки производственных процессов, без полной разборки-сборки оборудования для поиска конкретных неисправностей и т.д. |
Понятно, что система принятия решений, способная решать подобные задачи и постоянно обучаться на непрерывно накапливаемых данных, может уверенно функционировать только как облачный сервис. Также посредством облачных технологий будет осуществляться прозрачная интеграция в системы управления предприятий.
Автоматическое управление техническим состоянием оборудования с полной интеграцией в системы управления активами — это условие выживания концепций Индустрии 4.0 и IIoT.
Более того, задача автоматизации управления техническим состоянием смещается в сторону изготовителя производственного оборудования. Это подталкивает его к созданию оборудования с уже встроенными автоматическими системами. На автоматических заводах будущего нет места отделам диагностики.
Что выигрывает бизнес?
I. Повышение надёжности оборудования: предотвращение аварий, существенное увеличение ресурса оборудования, расширение межсервисных и межремонтных интервалов.
II. Освобождение производственных процессов от избыточности: исключение планово-предупредительных ремонтов, освобождение ресурсов, ранее занятых в избыточном обслуживании оборудования.
III. Полная интеграция технологических процессов с системами управления предприятий. Становится ближе технология полностью автоматического производства.
![]() |
Кроме этого, так обеспечивается доступ к полной истории функционирования оборудования — от ввода в эксплуатацию до появления проблемы, зарождения дефекта и вплоть до наступления отказа. RxM своевременно предписывает обслуживание (к примеру, замена загрязнившейся смазки), основываясь на актуальных данных о состоянии оборудования и его конкретных деталей. Это позволяет предельно уменьшить влияние факторов, сокращающих срок службы. Если что-либо угрожает преждевременным износом, RxM выдаёт предписания по изменению режимов функционирования оборудования. Когда в оборудовании что-либо стареет, изнашивается и вскоре выйдет из строя, RxM даёт информацию для подготовки запчастей и планирования ремонта без неожиданной остановки производственного процесса. Всё это автоматически документируется и позволяет контролировать использование оборудования во время гарантийного срока, зная условия и режимы его эксплуатации, а также причины отказов. |
По этому пути каждый идёт по-своему. Одни поглощают занимающиеся диагностикой компании, замыкая цепочку «оборудование — оценка технического состояния — управление техническим состоянием — система управления предприятием» в рамках холдинга. Другие для этого организовывают партнёрства, договариваясь о сотрудничестве.
2.3. Что мешает современной диагностике стать частью Индустрии 4.0?
В настоящее время происходит активное развитие интеллектуальных систем управления техническим состоянием оборудования, претендующих на место в Индустрии 4.0 и IIoT.
![]() |
Техническая возможность для воплощения систем технической диагностики и управления эксплуатацией и обслуживанием сложного оборудования в виде полностью автоматического сервиса появилась относительно недавно. Благодаря достижениям в области информационных технологий созданы эффективные облачные системы хранения и обработки информации и быстрые беспроводные каналы передачи больших данных. Появились новые способы обработки информации, такие как вейвлетный анализ, преобразование Гильберта-Хуанга, создание собственных базисов, машинное обучение, методы уменьшения размеров выборок. |
Однако велики и трудности, с которыми сталкиваются разработчики таких систем:
- Высокая цена ошибок в системе;
- Формирование и валидация обучающей выборки;
- Формирование пространства информативных признаков;
- Необходимость разрабатывать ряд дополнительных алгоритмов.
I. Цена ошибок в технологической системе
В Индустрии 4.0 функция эксперта становится наблюдающей, и в этих условиях требования к надёжности работы производственного оборудования чрезвычайно высоки.
Технологические системы по цене ошибок условно можно разделить на три группы:
- Цена единичных ошибок невелика. Хорошие примеры — это любые развлекательные системы. Не случится аварии и никто не пострадает, если приложения Prisma или Fabby отрисовали картинку не так, как хотелось. Не критично, если в тёмном (или слишком светлом) помещении допустит сбой алгоритм MSQRD.
- Цена единичных ошибок средняя. Классический пример — системы кредитного скоринга. Единичные ошибки в них неприятны, но и не исключены в повседневной практике (и заложены в систему как риски). Такие сценарии требуют глубокой проработки математических моделей, вдумчивой работы с обучающими выборками, выбором функции активации и т.д. Занимаются этим серьёзные научные коллективы, иногда целые кафедры ведущих учебных заведений.
- Цена единичных ошибок высока. Это — технологические системы, применяемые в медицине, добывающей и перерабатывающей промышленности, транспорте и т.д. В этих сферах обычно избегают применения нейронных сетей напрямую, в основном из-за неявности принятия решений и трудностей с устранением ошибок классификации. Именно поэтому много внимания уделяется формированию пространства информативных признаков для блоков машинного обучения, а также дополнению их более устойчивыми и прозрачными алгоритмами, например, на основе нечёткой логики (что позволяет имитировать работу эксперта с системой предположений и их проверкой).
II. Формирование и валидация обучающей выборки
Современные методы машинного обучения (в первую очередь, нейронные сети) требуют для инициализации большие объёмы обучающих выборок (training data sets).
Основной прогресс методов машинного обучения сейчас наблюдается в таких областях, как обработка изображений, речевые технологии, обработка текста, медицина (обработка медицинских изображений и работа с историей болезни). Объединяет эти области то, что большие объёмы правильно размеченных данных (обучающие выборки для алгоритмов машинного обучения) либо уже набраны и доступны, либо могут быть относительно легко подготовлены. Совсем иная ситуация в тех областях, где обучающих выборок нет либо они не могут быть быстро собраны и сформированы в необходимом объёме.
Вибродиагностика как часть системы RxM — одна из таких проблемных областей. В настоящее время не существует баз данных валидированных вибрационных сигналов, подготовленных для систем машинного обучения. Причина в том, что исторически вибродиагностика была экспертно-зависимой областью, где в первую очередь обучали эксперта, а не машину. Поэтому базы обучающих данных в виде исходных вибрационных сигналов просто не создавались.
Вторая часть проблемы связана с широчайшей номенклатурой механизмов по отраслям промышленности. Именно поэтому формирование и валидация исчерпывающей обучающей выборки для универсальных систем диагностики представляет собой чрезвычайно трудную задачу.
III. Формирование пространства информативных признаков
Алгоритмы машинного обучения решают задачу классификации объектов в пространстве информативных признаков. Это пространство представляет собой числовое описание объектов классификации в виде векторов значений, соответствующих некоторому набору признаков для данного объекта. Анализируя эти данные и обучаясь на них, алгоритмы машинного обучения относят объекты к каким-то заранее определённым классам.
Методы диагностики, широко использующиеся в настоящее время (метрические методы, а также спектр сигнала и спектр огибающей вибрационного сигнала) формируют пространство признаков дефектов оборудования в чрезвычайно неудобном для автоматических классификаторов виде. Основная проблема в том, что размерность данного описания чрезвычайно мала для устойчивой работы алгоритмов машинного обучения. Это связано с тем, что традиционные методы обработки вибрационного сигнала очень просты, были предложены более 50 лет назад и до сих пор широко применяются. Кроме того, вибродиагностика традиционно была экспертно-ориентированной, а человек физически не способен работать с пространством признаков большой размерности.
IV. Необходимость разрабатывать ряд дополнительных алгоритмов
Экспертно-ориентированные системы не нуждаются в некоторых алгоритмах, которые необходимы для работы полностью автоматических систем.
В качестве примера можно привести алгоритм уточнения частоты вращения валов механизма по вибрационному сигналу, предназначенный для слежения за частотой вращения роторных элементов механизма. Использование этого алгоритма позволяет автоматической системе диагностировать механизмы, работающие в нестационарном режиме (наиболее яркий пример — это транспортные средства).
Универсальный, хорошо масштабируемый облачный сервис RxM также не обойдётся без автоматического анализа кинематической схемы механизма. Это позволит формировать пространство признаков всех потенциальных дефектов отдельных элементов оборудования. Обычно эту «ювелирную» работу выполняют эксперты отдела вибродиагностики.
Эти и другие алгоритмы разработаны специалистами VibroBox и составляют важную часть интеллектуальной собственности проекта.
2.4. Что делает наш сервис уникальным?
В VibroBox применяются новейшие методы обработки и анализа вибрационных сигналов и данных телеметрии. Мы используем методы математического моделирования, облачные технологии хранения и обработки данных, вейвлетный анализ, создание собственных базисов, машинное обучение, алгоритмы нечёткой логики и многое другое.
Сейчас для решения таких задач, как правило, создаются стационарные системы диагностики. Их внедрение требует больших затрат на проведение научно-исследовательских работ с конкретным оборудованием. Результат этой работы — специализированные программно-аппаратные комплексы, основой работы которых служит ограниченный опыт команды создавших их экспертов. По этим причинам подобные решения не поддаются масштабированию и полностью лишены возможности самообучения.
Архитектура, методы обработки сигналов и принятия решений делают VibroBox универсальным и легко масштабируемым сервисом. Он постоянно обучается на достигаемых результатах, увеличивая их точность и информативность. Благодаря этому каждый новый пользователь получает результаты даже при первом использовании сервиса.
При всех преимуществах стоимость использования сервиса VibroBox на порядки ниже капитальных вложений на развёртывание и поддержку стационарных узкоспециализированных диагностических систем.
Сфера применения VibroBox не ограничивается одним лишь промышленным оборудованием. Уже сейчас интерес к нашему проекту проявляют обслуживающие организации и пользователи железнодорожных локомотивов и грузовых автомобилей.
VibroBox работает с виброакустическими сигналами, полученными любым доступным способом — вплоть до использования микрофона, встроенного в смартфон либо планшетный компьютер. Для этого нашей командой разработаны мобильные приложения для Android и iOS, которые имеют полноценный функционал обработки данных и выдачи готовых отчётов. Это — самый доступный инструмент для экспресс-диагностики вашего оборудования.
3. Как работает VibroBox
VibroBox — универсальная, легко масштабируемая технология для реализации предписывающего обслуживания производственного оборудования.
Принятие решений сервисом VibroBox основано на:
- глубокой аналитике текущего состояния оборудования, которая возможна благодаря объединению полученных вибрационных сигналов и данных телеметрии с виртуальной моделью оборудования (называемой также «цифровой двойник»)
- последующем прогнозировании состояния оборудования.
На базе облачных технологий VibroBox реализует современные методы анализа сигналов, такие как вейвлетный анализ (Wavelet Analysis), создание собственных базисов, машинное обучение (Machine Learning), алгоритмы нечёткой логики (Fuzzy Logic) и т.д.
VibroBox позволяет существенно сократить затраты на эксплуатацию и обслуживание оборудования, в том числе:
- существенно увеличить ресурс оборудования за счёт правильно и своевременно проводимого технического обслуживания;
- исключить аварийные ситуации и незапланированные простои;
- повысить продуктивность производства путём перехода от обслуживания оборудования «по регламенту» к обслуживанию «по состоянию»;
- оптимизировать производственные бизнес-процессы за счёт интеграции предписывающего обслуживания в систему управления предприятием (CMMS, MES, ERP);
- наладить автоматическое производство, в котором все операции контроля, прогнозирования и принятия решений выполняются без вмешательства человека;
- высвободить ресурсы, ранее занятые в избыточном операционном контроле и обслуживании оборудования.
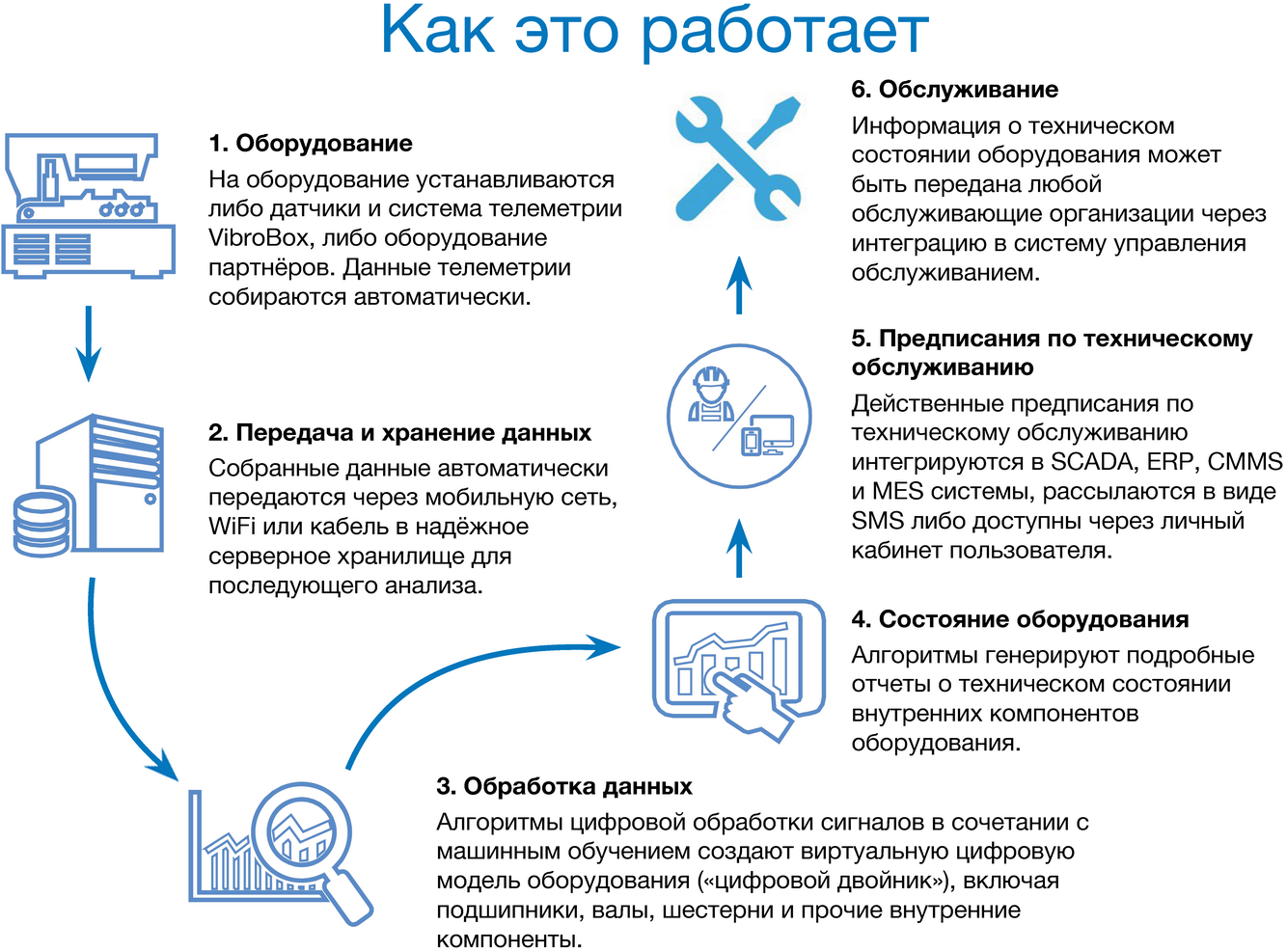
VibroBox анализирует получаемые от оборудования вибрационные сигналы и данные телеметрии (акустический сигнал, температура перегрева узлов, ток потребления двигателей и др.). На основе результатов анализа этих данных формируется оценка технического состояния оборудования и формируются предписания по эксплуатации оборудования и его обслуживанию.
Результаты работы предоставляются в виде подробных отчётов, доступных через личный кабинет пользователя. Также они могут направляться в системы управления активами (CMMS, MES, ERP).
Подробно принцип работы VibroBox описан в разделе «Концепция сервиса VibroBox».
4. Концепция сервиса VibroBox
Основная новизна VibroBox не в системах передачи данных и не в датчиках, а в способах обработки вибрационного сигнала и данных телеметрии, позволяющих формировать удобное пространство информативных признаков для работы классификаторов (машина на опорных векторах и нейронных сетей). Именно за счёт этого сервис становится автоматическим, а вибродиагностика приобретает новые возможности для решения задач в рамках промышленного интернета вещей (Industrial Internet of Things, IIoT) и Индустрии 4.0.
Алгоритмы оценки технического состояния оборудования, реализованные в VibroBox, отвечают за выделение наборов информативных признаков и решение задачи классификации по этому пространству признаков. Результат работы классификатора — определение состояния оборудования в рамках одного из классов, сформированных за счёт автоматического анализа кинематической схемы и оценки параметрической модели («цифрового двойника»). Так система определяет текущее состояние оборудования, включая проблемы его конкретных элементов. В соответствии с выявленным состоянием оборудования и динамикой его изменения VibroBox формирует предписания по его эксплуатации и техническому обслуживанию.
VibroBox функционирует как облачный сервис. Его алгоритмы — это отдельные программные серверы, которые обрабатывают данные и масштабируются независимо от остальных компонентов системы.
Многие алгоритмы, разработанные специалистами VibroBox, не существовали ранее. Это такие методы, как алгоритм уточнения и слежения за частотой вращения роторных компонентов оборудования по вибрационному сигналу, набор алгоритмов для анализа кинематической схемы механизма и др.
Принцип работы VibroBox представлен на рисунке 2.
Источники вибрационных сигналов и иных данных телеметрии передают первичную информацию в VibroBox. Это вибрационный или акустический сигнал, температура и другие данные.
Система обработки информации занимается обработкой поступающей информации, оценкой технического состояния оборудования и формированием предписаний по его эксплуатации и обслуживанию. Эта часть системы включает как вновь разработанные алгоритмы, так и традиционные методы.
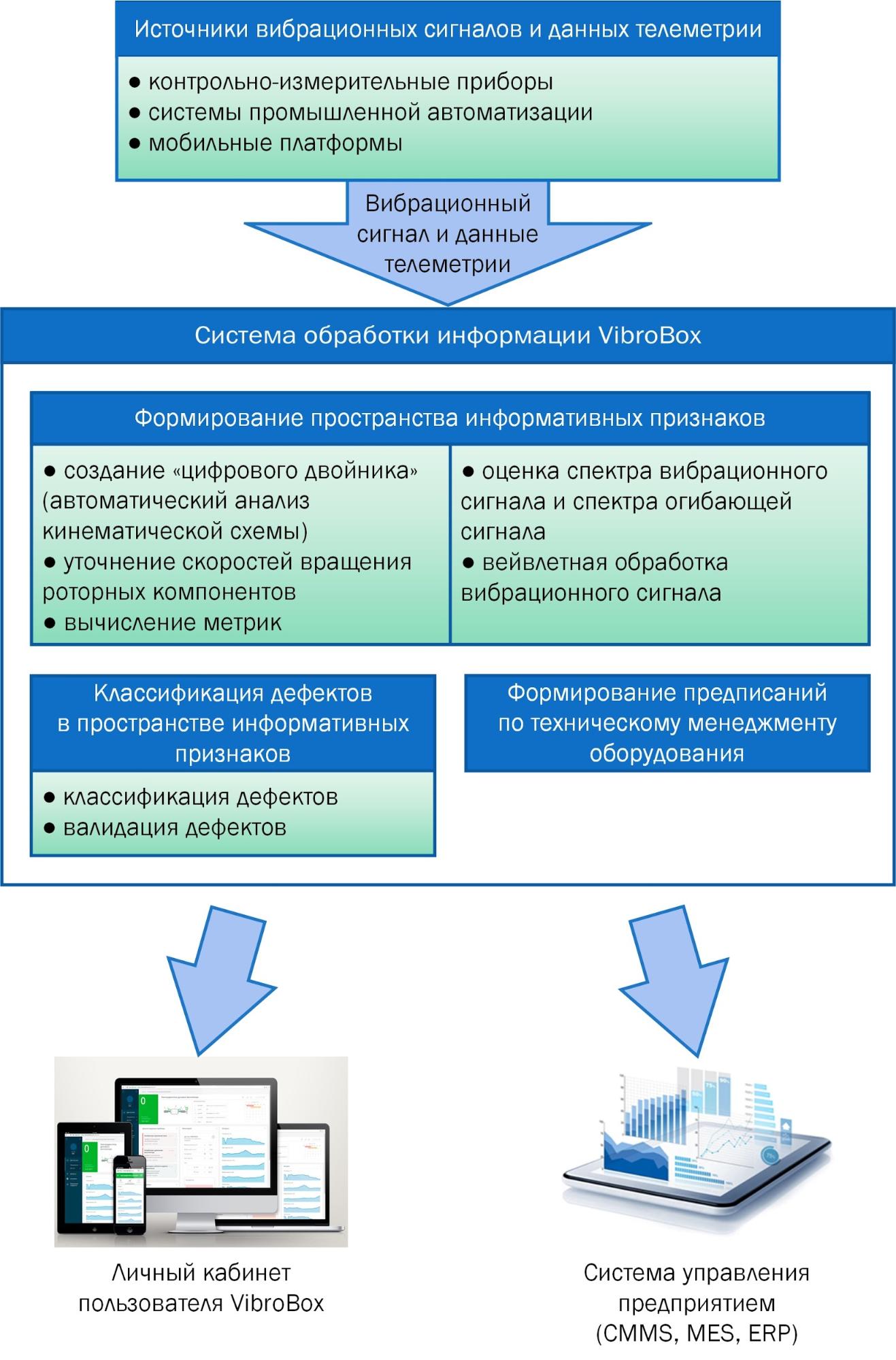
Задачи системы обработки информации:
- формирование пространства информативных признаков, в том числе:
- автоматический анализ кинематической схемы оборудования;
- уточнение скоростей вращения роторных компонентов оборудования;
- вычисление метрик;
- оценка спектра сигнала и спектра огибающей сигнала;
- вейвлетная обработка вибрационного сигнала;
- классификация дефектов в пространстве информативных признаков, состоящая из стадий:
- формирование предписаний по эксплуатации и обслуживанию оборудования.
Классификация дефектов оборудования в сформированном многомерном пространстве информативных признаков проводится алгоритмами, работающими на основе нейронной сети (Neural Network) и нечёткой логики (Fuzzy Logic). Результаты классификации являются результатами работы сервиса, представляя собой оценку технического состояния оборудования и предписания по его эксплуатации и обслуживанию.
Подробные результаты отображаются в личном кабинете пользователя и могут автоматически передаваться в систему управления предприятием (CMMS, MES, ERP).
5. Аппаратная платформа сервиса VibroBox
5.1. Общие сведения
Данные телеметрии могут передаваться сервису VibroBox из систем управления предприятия. Помимо этого VibroBox имеет собственную аппаратную платформу для получения вибрационных сигналов, температуры и других данных телеметрии непосредственно от оборудования. Съём сигналов производится специализированными датчиками, характеристики которых полностью удовлетворяют требованиям к качеству и полноте снимаемой телеметрической информации.
Также VibroBox поддерживает подключение датчиков вибрации других производителей (в частности, Bernecker + Rainer (B&R) и SKF), таких как акселерометры со встроенной электроникой ICP (IEPE), которые широко используются в системах промышленной автоматизации. Это позволяет VibroBox использовать для анализа сигналы от датчиков, уже встроенных в оборудование.
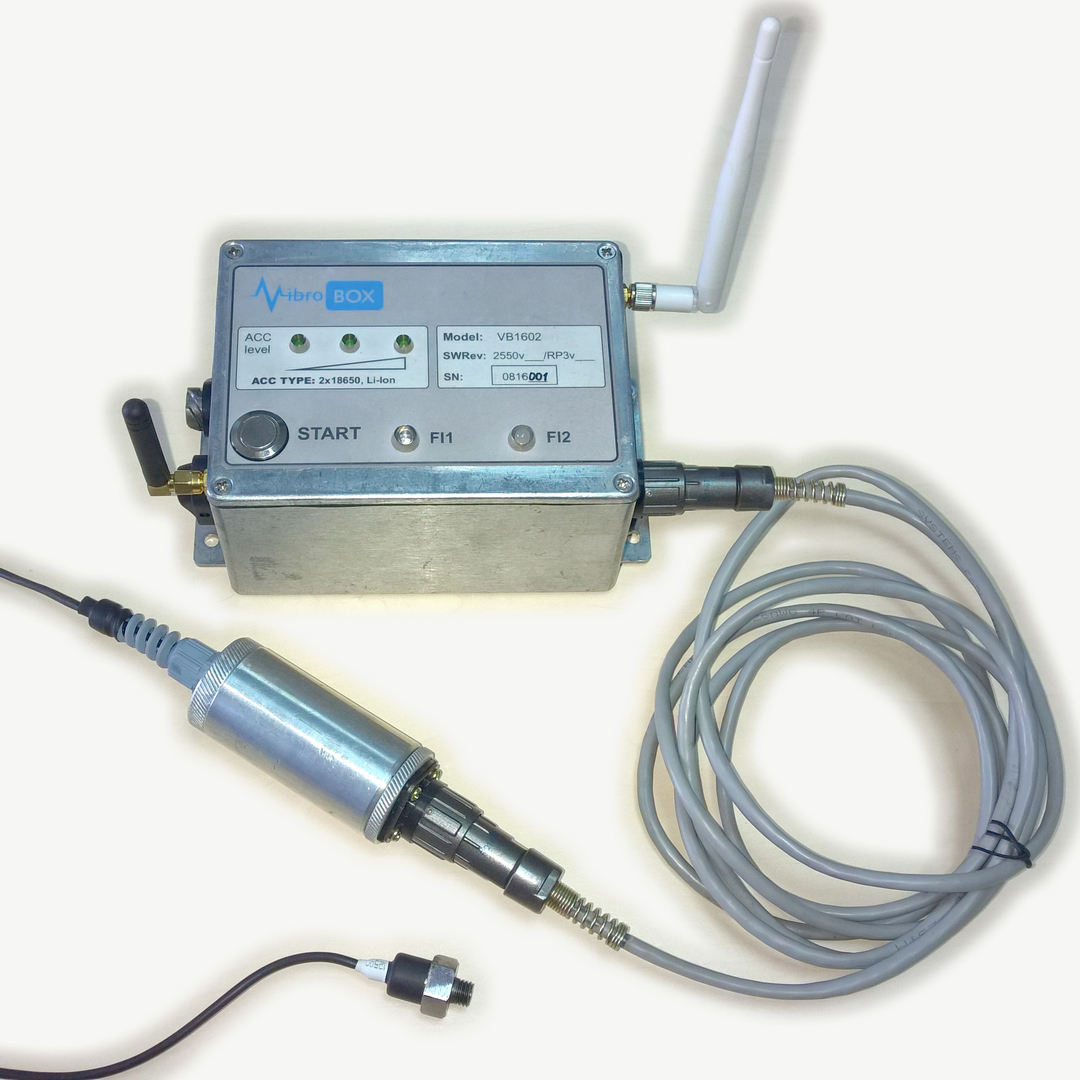
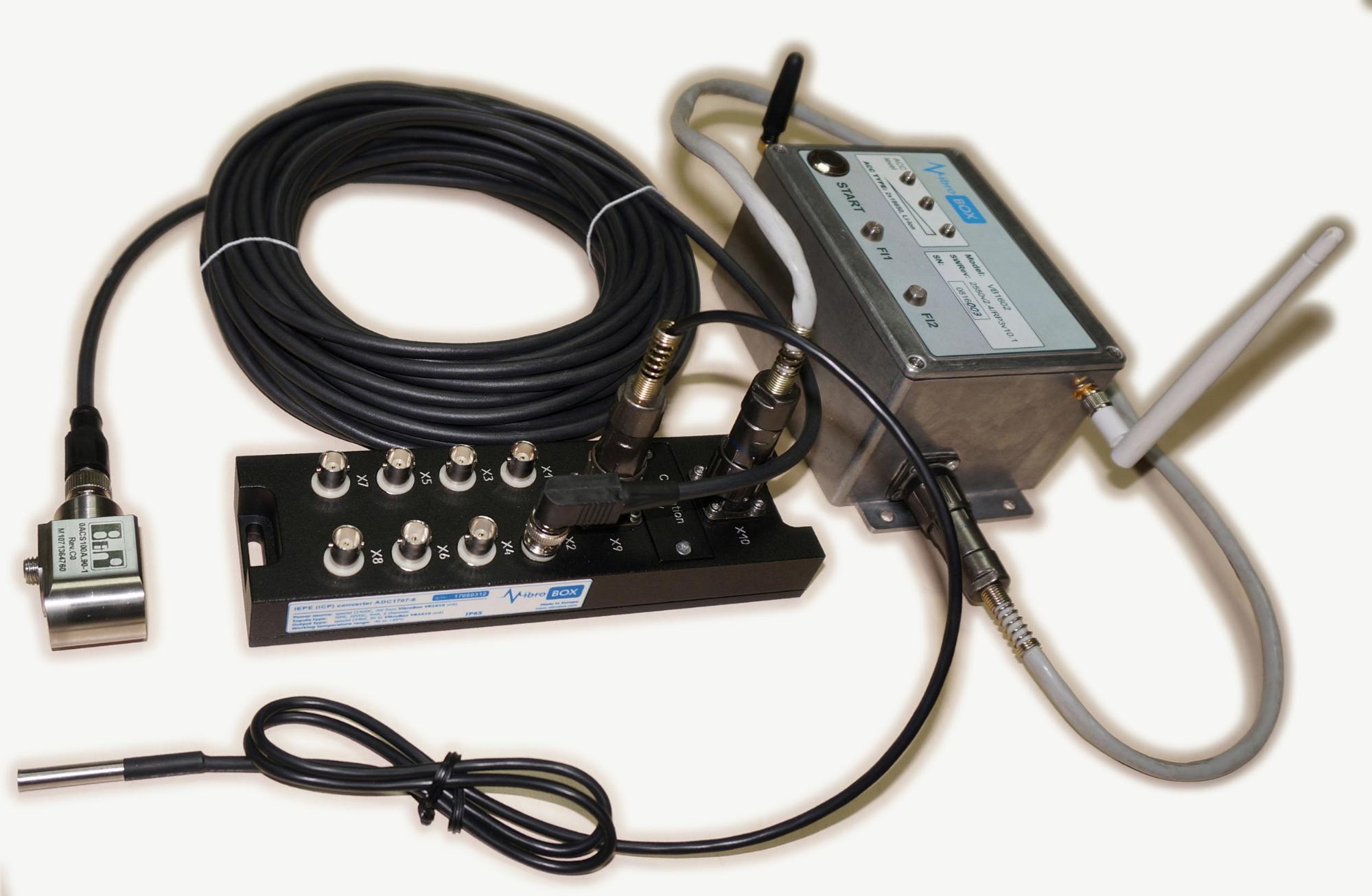
Более того, VibroBox позволяет использовать в качестве источников данных датчики вибрации и микрофоны, встроенные в современные смартфоны и портативные компьютеры. Полученные нашей командой результаты показывают, что во многих случаях диагностика оборудования по сценарию «приложить смартфон к оборудованию, записать вибрационный и акустический сигналы; передать их сервису VibroBox; получить и просмотреть отчёт на экране смартфона» получается достаточно информативной.
Все эти возможности дают пользователям VibroBox абсолютную свободу в выборе способа доставки данных для обработки.
5.2. Датчики для съёма вибрационного сигнала и данных телеметрии
Датчики вибрации VibroBox DVS предназначены для установки на оборудование с целью съёма данных посредством блока связи и передачи данных телеметрии. Предназначены для промышленной эксплуатации, не требуя дополнительного обслуживания и настройки.
Датчики VibroBox DVS (см. рисунок 5) имеют три конструктивных исполнения. Исполнения DVS1602/2Ch и DVS1610/2Ch состоят из первичного преобразователя ускорения (двухосевого MEMS-датчика), первичного преобразователя температуры и измерительного преобразователя, установленных в общем корпусе прямоугольной (исполнение DVS1602/2Ch) и цилиндрической (исполнение DVS1610/2Ch) формы.
Датчик DVS1703 состоит из двух частей:
- первая часть: содержит первичный преобразователь ускорения (двухосевой MEMS-датчик) и первичный преобразователь температуры, установленные в один цилиндрический корпус;
- вторая часть: содержит цифровой измерительный преобразователь, смонтированный во второй цилиндрический корпус.
Обе части соединены между собой кабелем, длина которого может быть изменена в зависимости от условий применения.
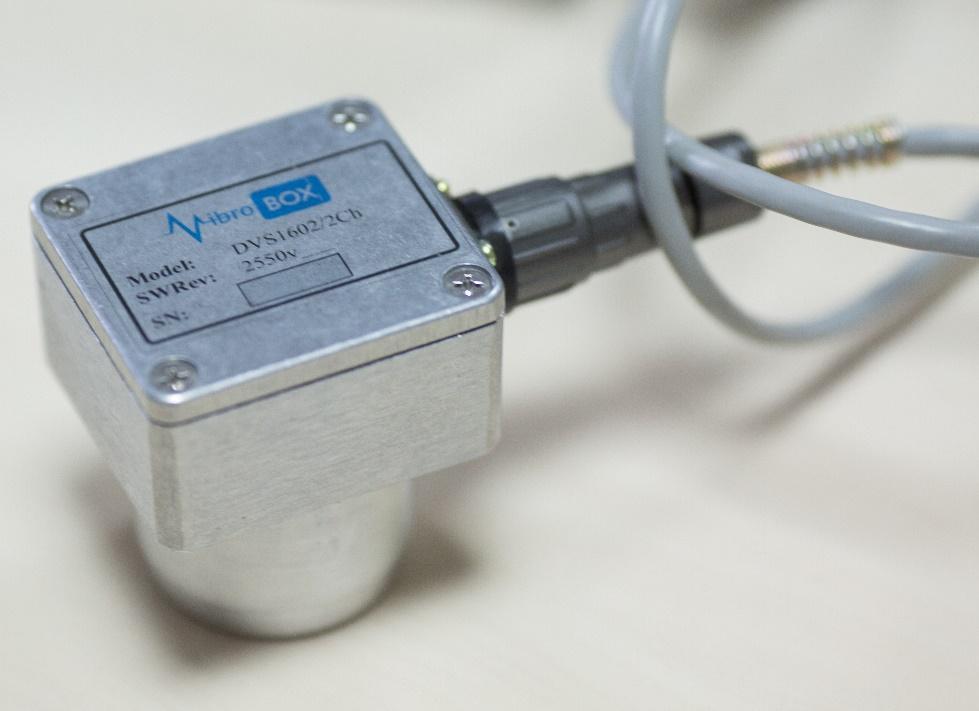
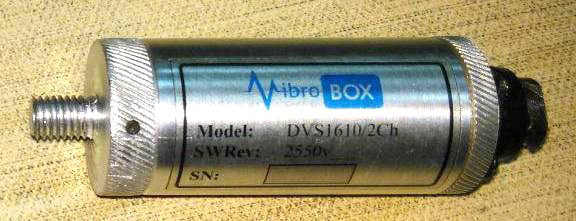
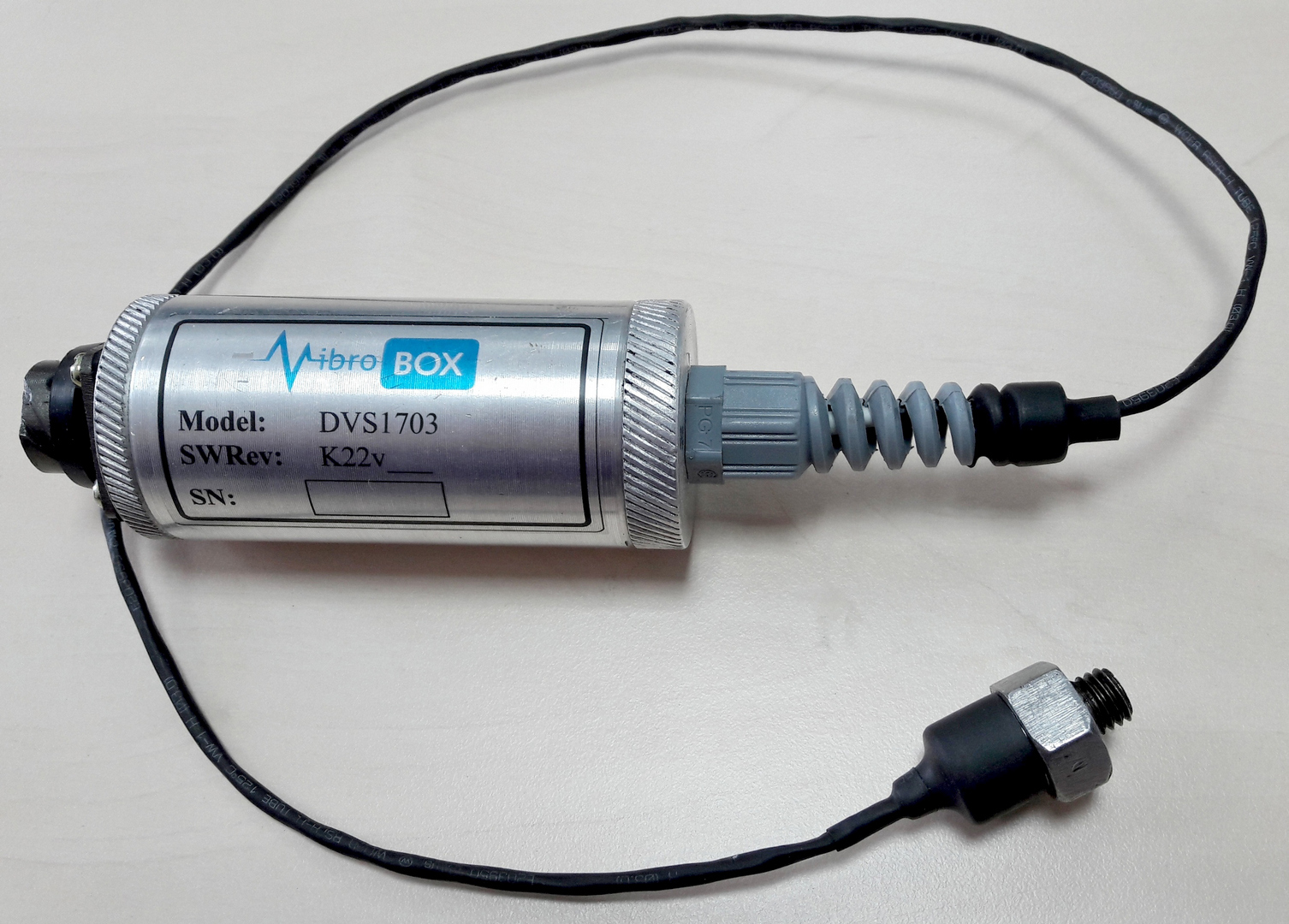
Рисунок 5 — Датчики вибрации VibroBox DVS.
Характеристики датчиков VibroBox DVS:
Наименование характеристики |
Значение характеристики |
Тип применяемого первичного преобразователя |
MEMS-датчик ускорения с диапазоном измерений ускорения ±70 g |
Диапазон измерения частот вибрации |
от 4 до 22 кГц |
Частота механического резонанса сенсора |
22 кГц |
Разрядность встроенного АЦП |
24 бит |
Частота дискретизации встроенного АЦП |
96 кГц |
Условия эксплуатации: |
|
климатическое исполнение |
УХЛ 1 по ГОСТ 15150-69 / CT по DS/IEC 721-2-1 |
диапазон рабочих температур * |
от минус 40 до +85°C |
Степень защиты оболочки |
IP67 (согласно IEC 60529-2004 / ГОСТ 14254-96) |
Тип крепления датчика на оборудование |
установка с помощью шпильки с метрической резьбой |
Габаритные размеры: |
|
исполнение DVS1602/2Ch |
80 × 60 × 55 мм (Ширина × Глубина × Высота) |
исполнение DVS1610/2Ch |
95 × 35 мм (Длина × Диаметр) |
исполнение DVS1703: |
|
часть с первичными преобразователями |
24 × 17 мм (Длина × Размер «под ключ») |
часть с измерительным преобразователем |
93 × 35 мм (Длина × Диаметр) |
Масса датчиков (без учёта кабеля): |
|
исполнение DVS1602/2Ch |
0,16 кг |
исполнение DVS1610/2Ch |
0,16 кг |
исполнение DVS1703 |
0,2 кг |
___________ * уточнение климатического исполнения |
Установка датчиков на оборудование осуществляется при помощи встроенной стальной шпильки с метрической резьбой. Также возможна установка датчиков с применением магнитных держателей (см. рисунок 6), используемый при невозможности для применения резьбового соединения с оборудованием.
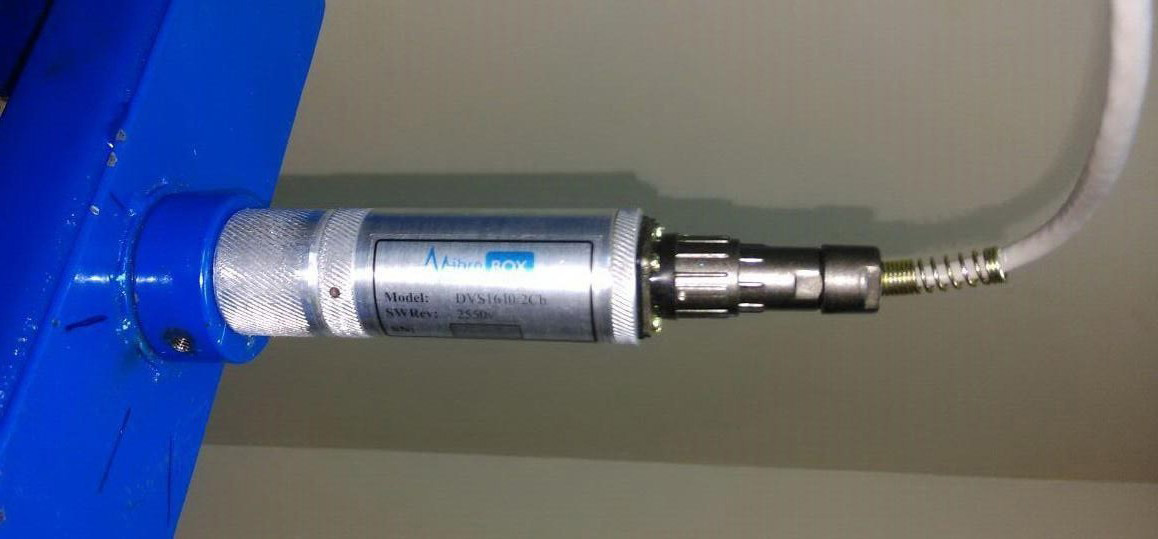
5.3. Блок связи и передачи данных телеметрии
Блок связи и передачи данных телеметрии VibroBox VB1610 предназначен для обработки сигналов с подключаемых к нему источников вибрационных сигналов и данных телеметрии, формирования пакетов кодированной информации и передачи её на серверы VibroBox посредством цифровых каналов связи. Общий вид блока приводится на рисунке 7.
В качестве источников сигналов к блоку VB1610 могут быть подключены датчики VibroBox DVS либо ICP (IEPE)-конвертер VibroBox.
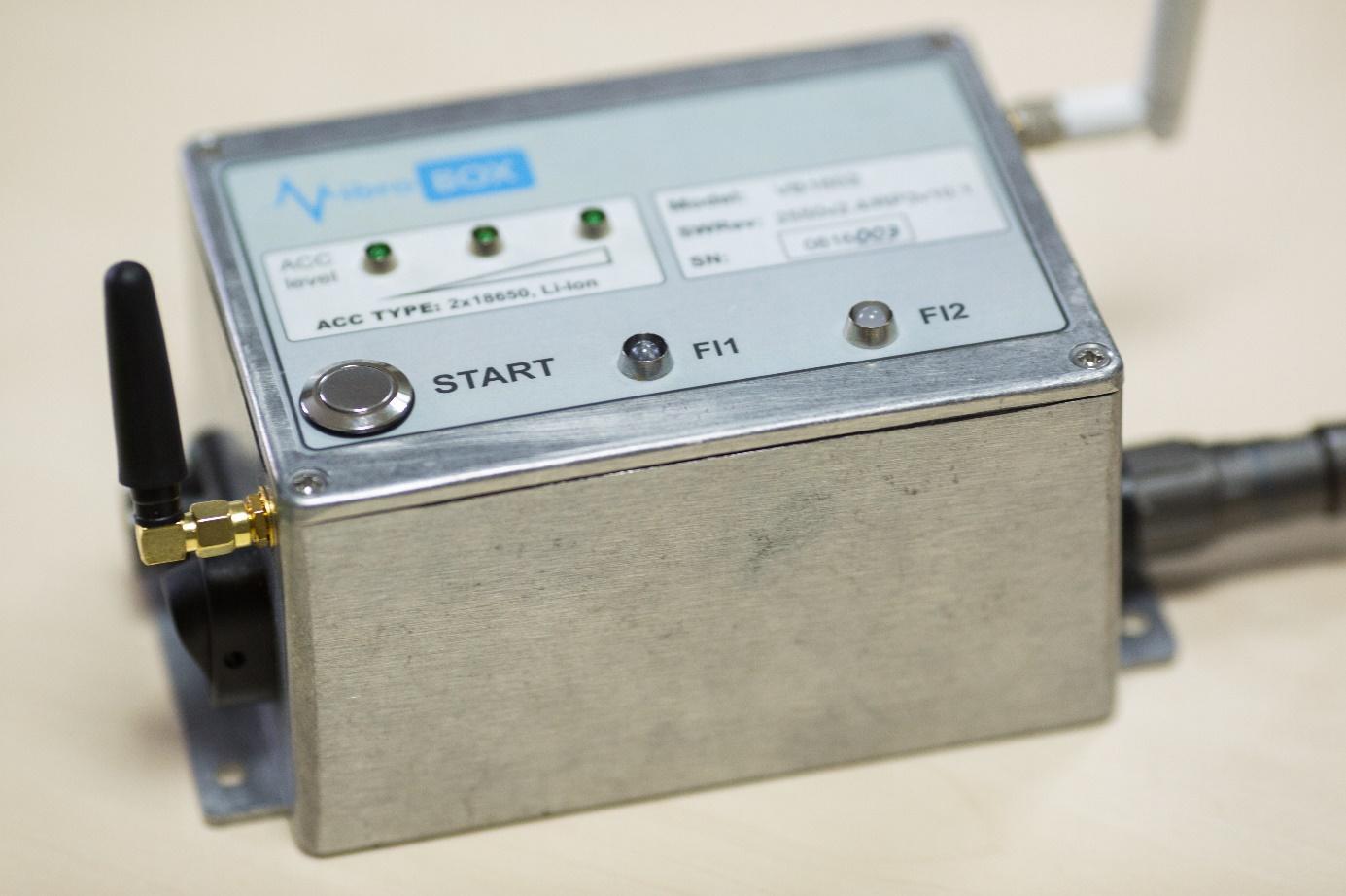
Характеристики блока VB1610:
Наименование характеристики |
Значение характеристики |
Характеристики электропитания: |
|
напряжение источника питания постоянного тока |
от 12 до 36 В |
напряжение сети переменного тока (возможно подключение с использованием внешнего блока питания) |
от 100 до 240 В |
мощность потребления |
15 Вт |
тип встроенных аккумуляторных батарей |
Li-Ion |
время автономной работы (при отсутствии внешнего электропитания) |
не менее 3-х часов в режиме постоянного измерения |
Количество входов для подключения источников сигнала |
1 шт. |
Типы поддерживаемых источников сигнала |
|
Интерфейсы связи: |
|
встроенный модуль WiFi |
|
3G-модем: |
|
стандарты |
UMTS/HSUPA/HSPA + GSM/GPRS/EDGE |
скорость передачи данных |
21,6 Мбит/с (HSDPA), 5,76 Мбит/с (HSUPA) |
Условия эксплуатации: |
|
климатическое исполнение |
УХЛ 1 по ГОСТ 15150-69 / CT по DS/IEC 721-2-1 |
диапазон рабочих температур * |
от +5 до +40°C |
Степень защиты оболочки |
IP65 (согласно IEC 60529-2004 / ГОСТ 14254-96) |
Габаритные размеры (Ширина × Глубина × Высота, без учёта выступающих антенн) |
170 × 102 × 81 мм |
Масса блока |
1 кг |
___________ * уточнение климатического исполнения |
5.4. ICP (IEPE)-конвертеры VibroBox
ICP (IEPE)-конвертеры VibroBox предназначены для конвертирования сигналов, снимаемых с подключаемых к нему акселерометров ICP (IEPE), и последующей их передачи в блок связи и передачи данных телеметрии VibroBox.
Характеристики ICP (IEPE)-конвертеров VibroBox:
Наименование характеристики |
Значение характеристики |
Характеристики электропитания: |
|
источник питания |
|
мощность потребления |
2 Вт |
Количество входов для подключения источников сигнала |
от 2 до 8 |
Тип поддерживаемого источника сигнала |
|
Условия эксплуатации: |
|
климатическое исполнение |
УХЛ 1 по ГОСТ 15150-69 / CT по DS/IEC 721-2-1 |
диапазон рабочих температур * |
от минус 40 до +85°C |
Степень защиты оболочки |
IP32 или IP65 (согласно IEC 60529-2004 / ГОСТ 14254-96) |
Габаритные размеры (Ширина × Глубина × Высота): |
|
двухканальный |
142 × 67 × 60 мм |
восьмиканальный |
150 × 60 × 47 мм |
Масса блока: |
|
двухканальный |
0,15 кг |
восьмиканальный |
0,4 кг |
___________ * уточнение климатического исполнения |
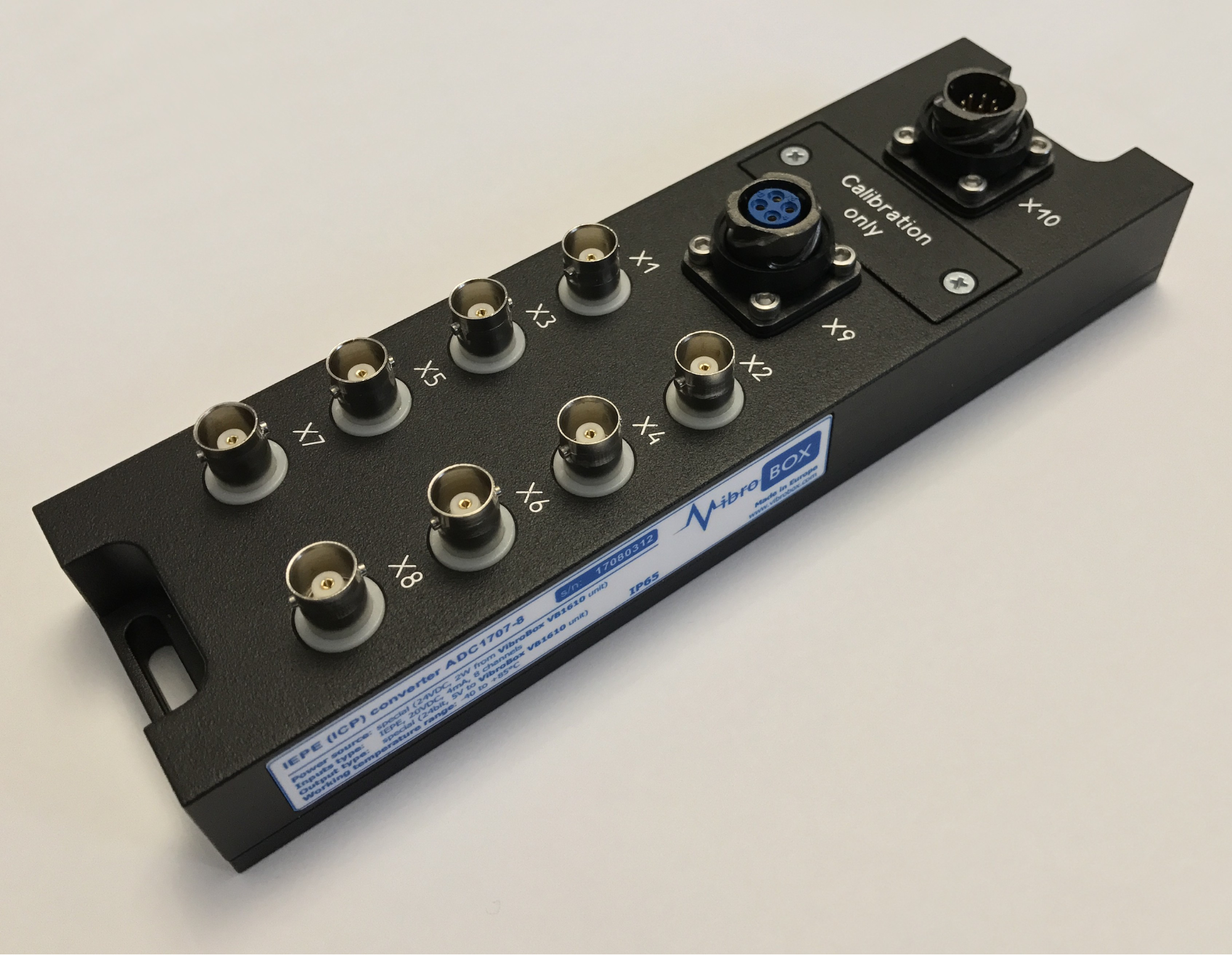
5.5. Блок съёма данных телеметрии для монтажа на DIN рейку
Блок снятия данных телеметрии предназначен для монтажа на DIN-рейку. Общий вид блока модели VB5.01-2ICP-DIN приводится на рисунке 9.
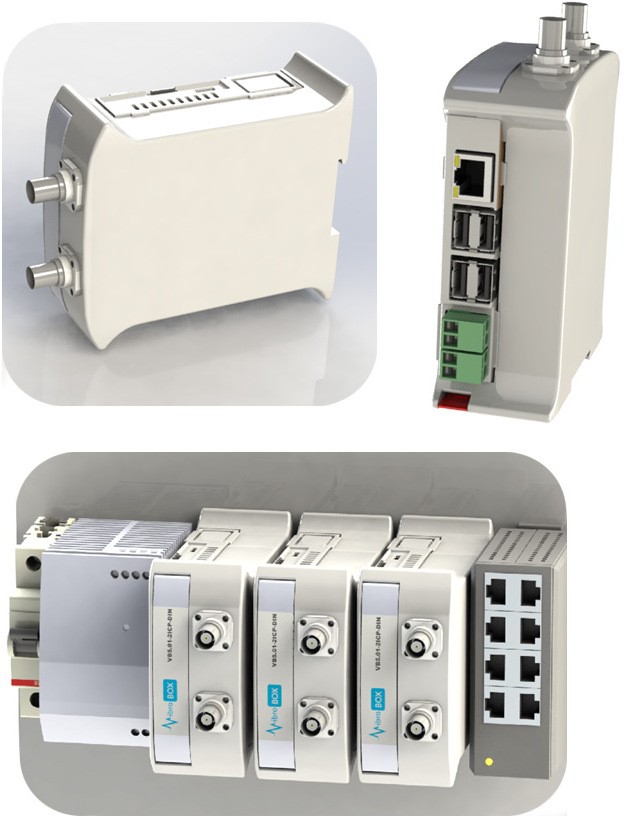
Характеристики блока съёма данных телеметрии VibroBox VB5.01-2ICP-DIN:
Наименование характеристики |
Значение характеристики |
Характеристики электропитания: |
|
тип электропитания |
источник питания постоянного тока |
напряжение источника питания |
24 В |
мощность потребления |
15 Вт |
Входы для подключения датчиков: |
|
количество входов |
2 |
тип подключаемого датчика |
акселерометр ICP (IEPE) |
Разрядность АЦП |
24 бит |
Частота дискретизации встроенного АЦП |
96 кГц |
Тип карты памяти |
microSD |
Объём памяти для программ |
16 ГБ |
Объём оперативной памяти |
1 ГБ |
Тип процессора |
Quad-Core ARMv8 Cortex-A53 64 bit |
Частота процессора |
1,2 ГГц |
Интерфейсы связи: |
|
встроенный модуль WiFi |
|
Bluetooth |
|
Ethernet |
100 Мбит/с |
количество портов USB |
4 |
Поддержка внешних USB устройств |
есть |
Условия эксплуатации: |
|
климатическое исполнение |
УХЛ 3.1 по ГОСТ 15150-69 / CT по DS/IEC 721-2-1 |
диапазон рабочих температур * |
от 0 до +55°C |
Степень защиты оболочки |
IP20 (согласно IEC 60529-2004 / ГОСТ 14254-96) |
Габаритные размеры (Ширина × Глубина × Высота) |
46 × 135 × 105 мм |
Тип крепления |
на DIN-рейку |
Масса блока |
0,2 кг |
___________ * уточнение климатического исполнения |
6. Система обработки информации сервиса VibroBox
Среди ключевых предпосылок, определяющих архитектуру VibroBox:
- место вибродиагностики в рамках промышленного интернета вещей и Индустрии 4.0;
- технические трудности, мешающие современной вибродиагностике стать частью Индустрии 4.0;
- потребность в интеграции процесса диагностики с системой управления предприятием (CMMS, MES, ERP).
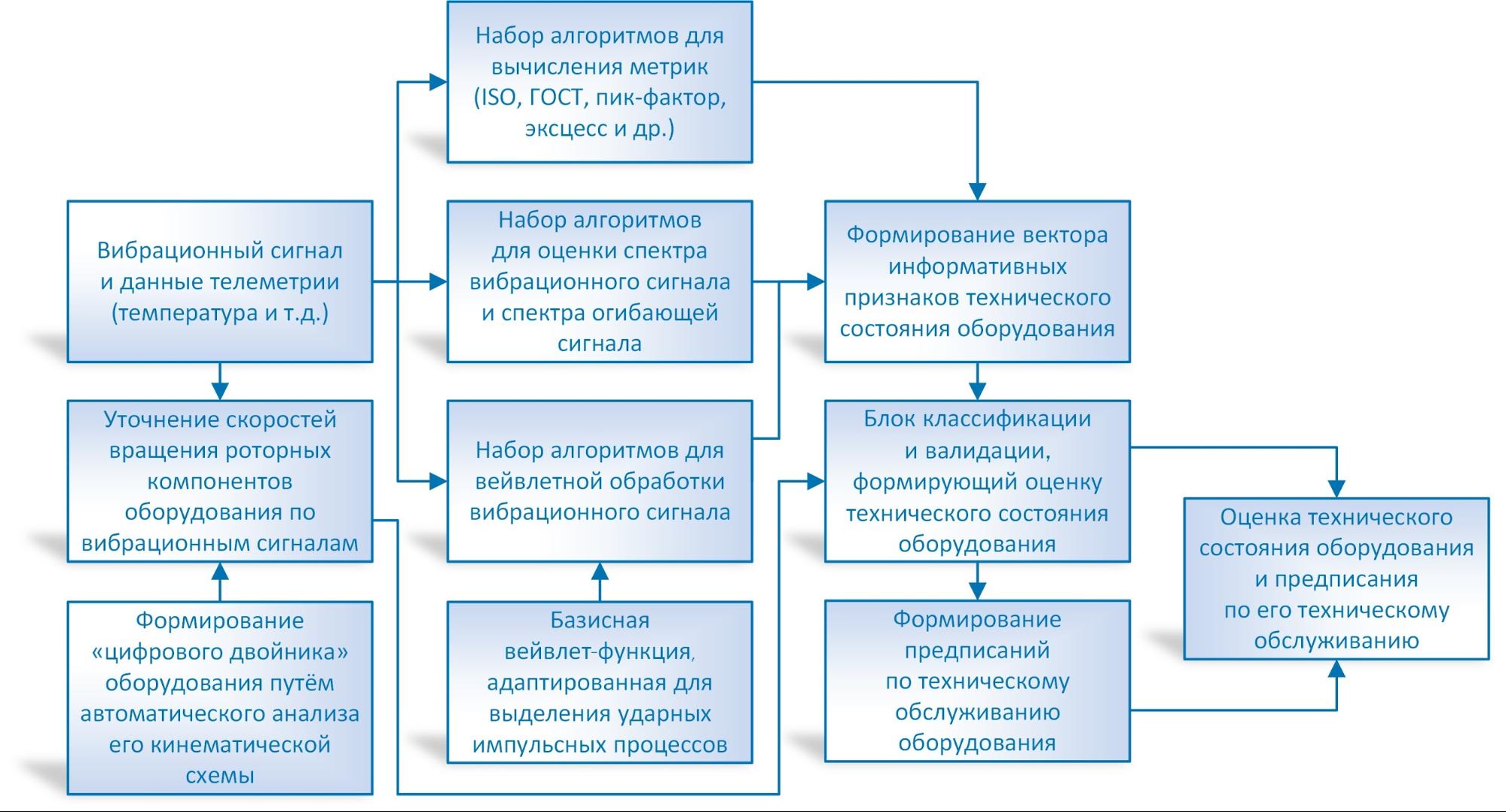
Обработка данных телеметрии производится на основе и при помощи следующих основных данных, функциональных частей и методов:
- вибрационный сигнал и данные телеметрии;
- формирование «цифрового двойника» оборудования путём автоматического анализа кинематической схемы оборудования;
- блок уточнения скоростей вращения роторных компонентов оборудования по вибрационным сигналам;
- набор алгоритмов для вычисления метрик (ISO, ГОСТ, пик-фактор, коэффициент эксцесса и др.);
- набор алгоритмов для оценки спектра и спектра огибающей вибрационного сигнала;
- набор алгоритмов для вейвлетной обработки вибрационного сигнала;
- базисная вейвлет-функция, адаптированная для выделения ударных импульсных процессов;
- вектор информативных признаков технического состояния оборудования;
- блок классификации (нейронная сеть) и валидации (нечёткая логика), формирующий оценку технического состояния оборудования;
- формирование предписаний по эксплуатации и обслуживанию оборудования.
6.1. Вибрационный сигнал и данные телеметрии
Для решения своих задач VibroBox анализирует вибрационные сигналы и данные телеметрии. Они могут сниматься датчиками VibroBox, а также датчиками других производителей (к примеру, акселерометры ICP (IEPE), широко применяемые в промышленности). VibroBox может обрабатывать данные, получаемые от автоматизированных систем управления предприятий, а также виброакустические сигналы с любых портативных устройств.
Задача оценки технического состояния промышленного оборудования по вибрационным сигналам имеет давнюю историю. В начале средства измерения и оценки информативных признаков дефектов были развиты слабо, и вибрационный сигнал оценивали интегрально, одной метрикой — среднеквадратичным уровнем, или, например, пик-фактором. Наиболее универсальные метрики и сейчас включены в ряд международных промышленных стандартов, регламентирующих техническую диагностику промышленного оборудования.
Учитывая это, мы вооружили VibroBox блоками расчёта большого количества стандартных метрик. С одной стороны, они используются для слежения за оборудованием в режиме мониторинга. С другой стороны — все рассчитанные метрики участвуют в формировании вектора информативных признаков технического состояния оборудования, по которому работает классификатор на основе нейронных сетей (Neural Networks) и нечёткой логики (Fuzzy Logic).
6.2. Блок автоматического анализа кинематической схемы оборудования
Кинематическая схема содержит информацию о конструкции оборудования и служит для формирования пространства информативных признаков его технического состояния. Пример кинематической схемы приводится на рисунке 11.
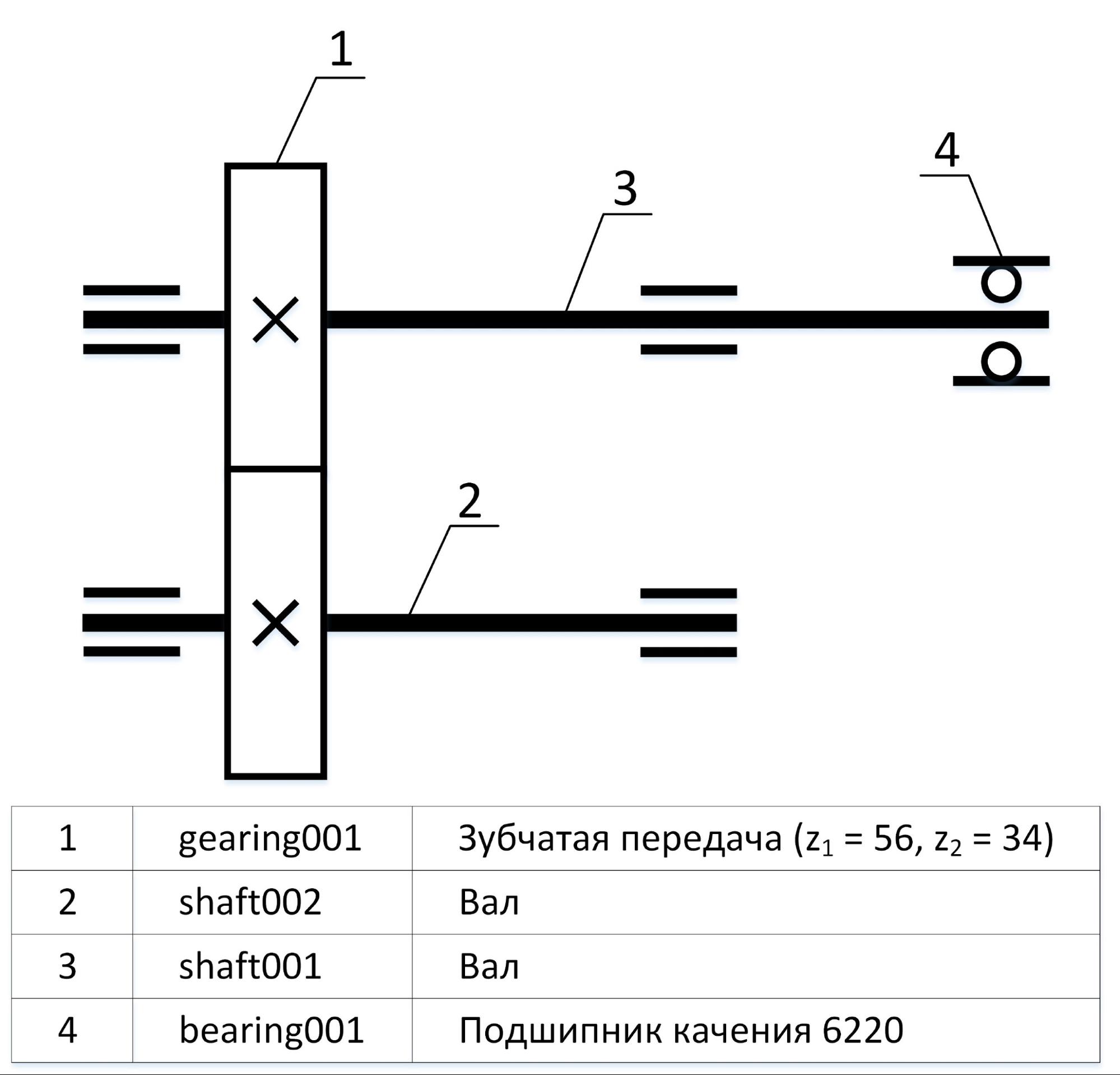
Для решения задач Prescriptive Maintenance важно знать, какие компоненты конструкции механизма принимают участие в передаче движения от двигателя к рабочим органам машины. Эти компоненты (зубчатые колеса, ходовые винты, валы, шкивы, муфты, подшипники и др.) принимают на себя механические нагрузки, изнашиваются и выходят из строя. Поэтому информация об их характеристиках и взаимодействии крайне важна для надёжной работы VibroBox.
Сервис VibroBox содержит специализированный программный блок, способный превратить кинематическую схему оборудования в его математическую модель — «цифровой двойник». Определённые таким образом наборы информативных признаков в дальнейшем используются для обучения классификаторов (нейронных сетей) и поиска соответствующих дефектов в вибрационном сигнале.
Для достижения максимальной гибкости и полной автоматизации сервиса мы работаем над алгоритмами, с помощью которых можно с высокой точностью определять тип оборудования и кинематическую схему механизма по его виброакустическим сигналам.
6.3. Блок уточнения скоростей вращения роторных компонентов оборудования по вибрационным сигналам
Любое промышленное оборудование имеет в своём составе набор роторных компонентов, передающих вращение от одних узлов к другим. Большинство дефектных частот вибрационных сигналов привязаны к частотам вращения этих узлов.
Отсутствие информации о скоростях вращения порождает серьёзную проблему для вибродиагностики: сетка дефектных частот подвергается искажениям (сжатиям/растяжениям), и отсутствие механизма адаптации пространства информативных признаков к этим искажениям увеличивает вероятность ложной тревоги или пропуска дефекта. Особенно явно это проявляется при постоянно меняющихся режимах работы оборудования.
Для определения точной скорости вращения конкретного вала лишь паспортных данных оборудования недостаточно. Поэтому для слежения за скоростями вращения специалисты по вибродиагностике используют дополнительные датчики.
VibroBox для автоматизации этой задачи пошёл гораздо дальше. Частоты вращения выделяются и уточняются по вибрационному сигналу. Делают это специализированные алгоритмы. Это позволяет снизить до минимума риски некорректного определения частот, связанные с применением сторонних аппаратных решений.
Графическая интерпретация примеров уточнения частоты вращения на основе анализа вибрации для двух типов оборудования приводится на рисунках 12 и 13.
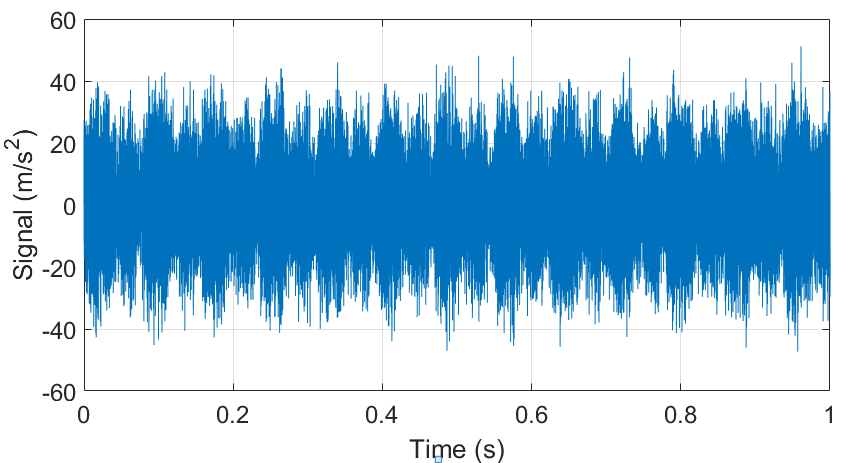
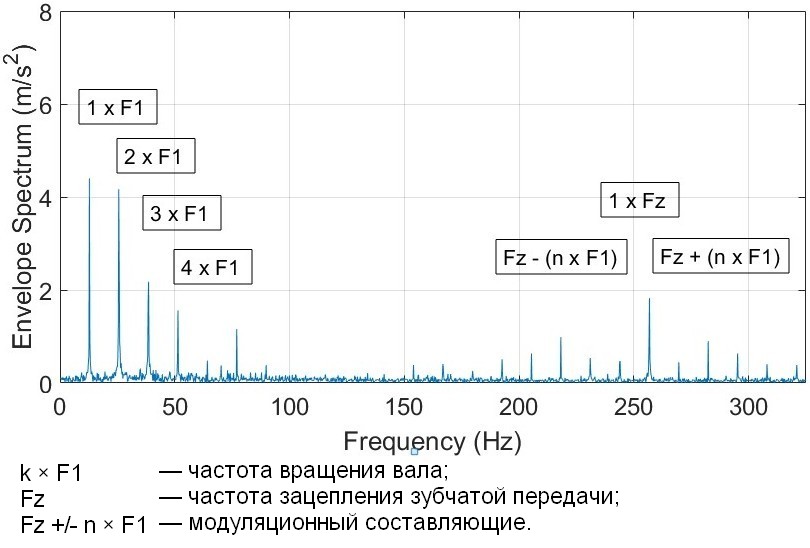
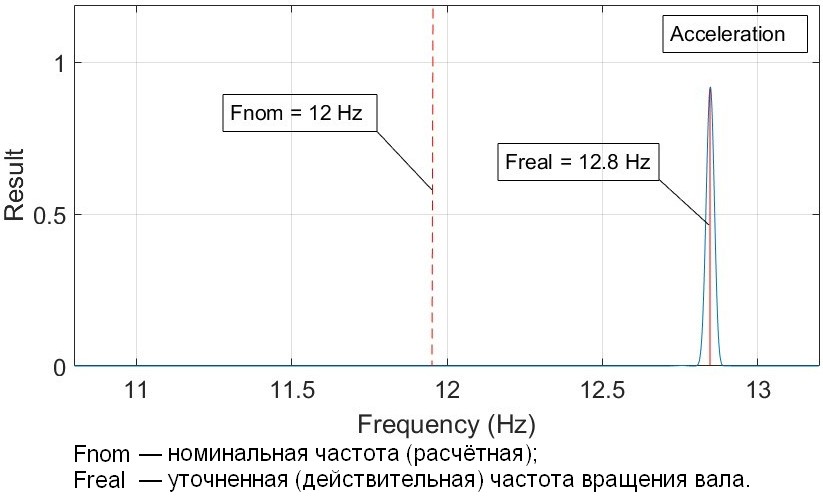
Рисунок 12 — Пример уточнения частоты вращения вала редуктора с зубчатой передачей на основе анализа вибрации.
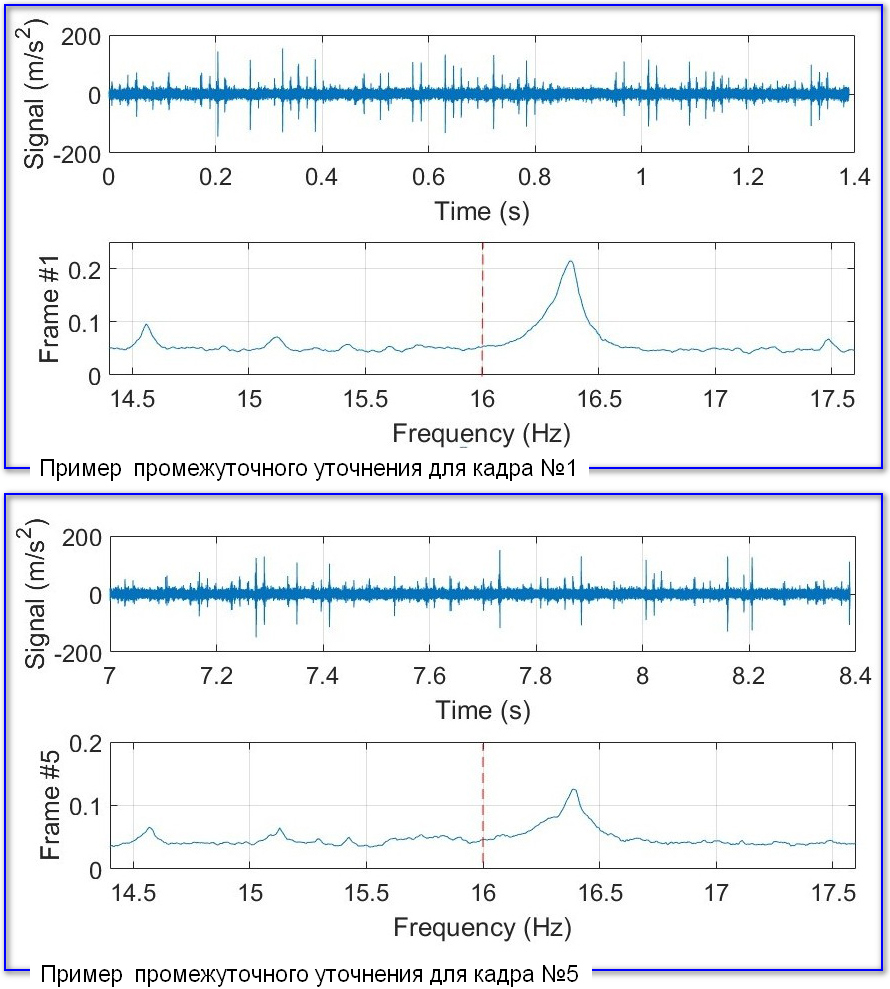
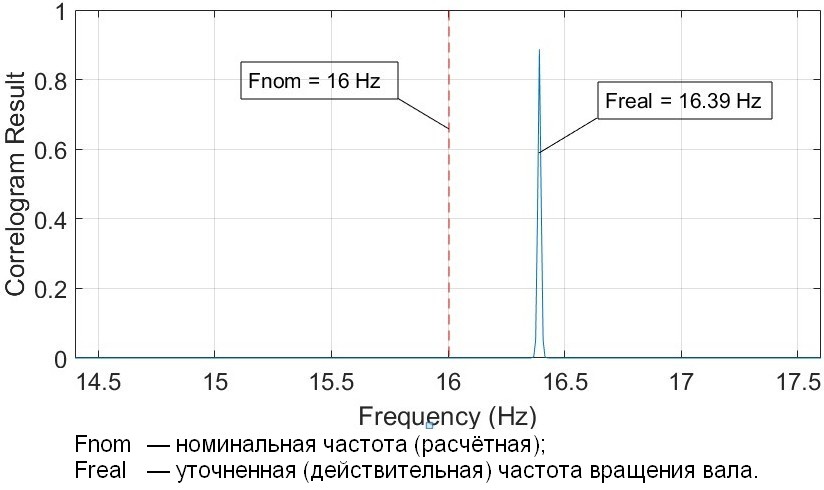
Рисунок 13 — Пример уточнения частоты вращения подшипника качения с дефектом наружного кольца на основе анализа вибрации.
6.4. Набор алгоритмов для вычисления метрик (ISO, ГОСТ, пик-фактор, коэффициент эксцесса и т.д.)
Метод диагностики по общему уровню (ISO, ГОСТ)
Данный метод регламентируется, в частности, стандартами серий ISO 10816-X (ISO 20816-X), ГОСТ ИСО 10816-X и ходит в широко распространённые технологии простейшей оценки технического состояния оборудования по общему уровню вибросигнала. Этот метод диагностики часто применяют заводы-изготовители оборудования для решения задач выходного контроля своей продукции. Реализуется измерением виброускорения элементов конструкции механизма на испытательном стенде (обычно в децибелах). Чем сильнее вибрация, тем тревожнее картина.
Критерии степени развития дефектов в данном методе полностью ориентированы на соответствующие нормированные уровни вибрации, принятые для данного механизма. При превышении порогового значения уровня вибрации обслуживающему персоналу либо системе мониторинга необходимо принимать решение о возможности дальнейшей работы агрегата или об остановке оборудования.
Несмотря на позднее обнаружение дефектов этот метод оценки технического состояния промышленного оборудования широко используется на практике и даёт хорошие результаты в тех случаях, когда:
- основной задачей проведения диагностического обследования является только предотвращение аварий, пусть даже проблема становится известной на позднем этапе;
- остановка оборудования и внеплановый ремонт могут быть выполнены в оставшееся до аварии время без нарушения технологического процесса.
Пример диагностики двигателя (мощность до около 15 кВт) согласно ISO 10816 показан на рисунке 14.
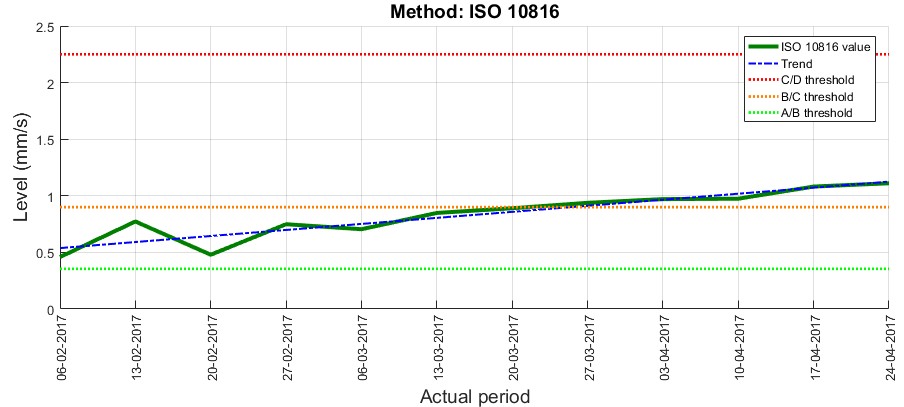
Диагностика с использованием метода пик-фактора
Это метод оценки технического состояния оборудования, основанный на анализе соотношений пиков и общего уровня (например, среднеквадратического значения) вибрации. Существует достаточно большое количество разновидностей этого метода, в разных литературных источниках данный метод часто объединяют с методом «ударных импульсов».
Базовое выражение для расчёта пик-фактора:

В процессе эксплуатации оборудования два этих параметра измеряются с высокой периодичностью. С течением времени, по мере появления дефектов на кинематических узлах оборудования, в вибросигнале начнут появляться отдельные короткие амплитудные пики, соответствующие моментам ударных процессов. В дальнейшем, с развитием дефекта, вначале увеличиваются амплитуды пиков, потом постепенно увеличивается и их количество. По мере появления и развития дефекта, нарастает амплитуда пиков, а среднеквадратичное значение меняется очень мало, поскольку отдельные, очень короткие амплитудные пики практически не меняют энергетические характеристики сигнала.
В дальнейшем, по мере увеличения количества пиков, начинает увеличиваться энергия сигнала, возрастает среднеквадратичное значение вибрации. Отношение амплитуды пиков к среднеквадратичному значению, называемое пик-фактором, представляет значительный интерес, поскольку эта функция имеет явно выраженный максимум на временнóй оси. На этом и основывается метод пик-фактора. Разновидности метода разрабатывались разными научными коллективами, поэтому несколько по-разному проводится сравнение уровней пика и фона вибросигнала. В одном случае для сравнения берётся амплитуда пика, в другом — энергия, фоновый уровень вибрации тоже может рассчитываться по-разному.
Главное достоинство метода — простота. Использование обобщённого количественного соотношения двух величин по типу «средний уровень — пик» позволяет определять техническое состояние механизма в целом. Из недостатков следует отметить слабую помехозащищённость метода и необходимость проводить многократные измерения в процессе эксплуатации. Сигнал вибрации характеризует механизм в целом, и чем сложнее кинематика механизма, тем меньше достоверность метода.
Диагностика по методу «ударных импульсов»
Этот метод является результатом некоторого развития методов пик-фактора и имеет несколько модификаций и наименований, в зависимости от того, какой коллектив доводил его до практического внедрения: HFD (High Frequency Detection[1]) — метод обнаружения высокочастотного сигнала, SPM (Shock Pulse Measurement) — метод измерения ударных импульсов, SE (Spike Energy[2]) — метод измерения энергии импульса.
Ударные процессы, возникающие из-за дефектов подшипника, вызывают генерирование высокочастотных, быстро затухающих колебаний, распространяющихся от подшипника по конструкциям механизма. Подшипниковые узлы при ударных процессах «звенят» на своей частоте. Частота эта практически всегда лежит в диапазоне от 28 до 32 кГц. Эти высокочастотные колебания быстро затухают, поэтому на осциллограммах выглядят практически как импульсы, что и дало название методу — метод ударных импульсов.
Амплитуды ударных импульсов связаны со скоростью вращения вала, действующей нагрузкой и степенью развития дефектов. Результаты измерений нормируются по скорости соударения, зная геометрию подшипника и скорость вращения вала. Таким образом, по амплитудам ударных импульсов можно диагностировать наличие и степень развития дефектов. При этом пороговые значения, характеризующие то или иное состояние подшипника, оказываются в общем случае универсальными, т.е. не зависят от типа и скорости вращения подшипника, хотя зависят от нагрузки.
Пример диагностики с использованием метода SPM приводится на рисунке 15.
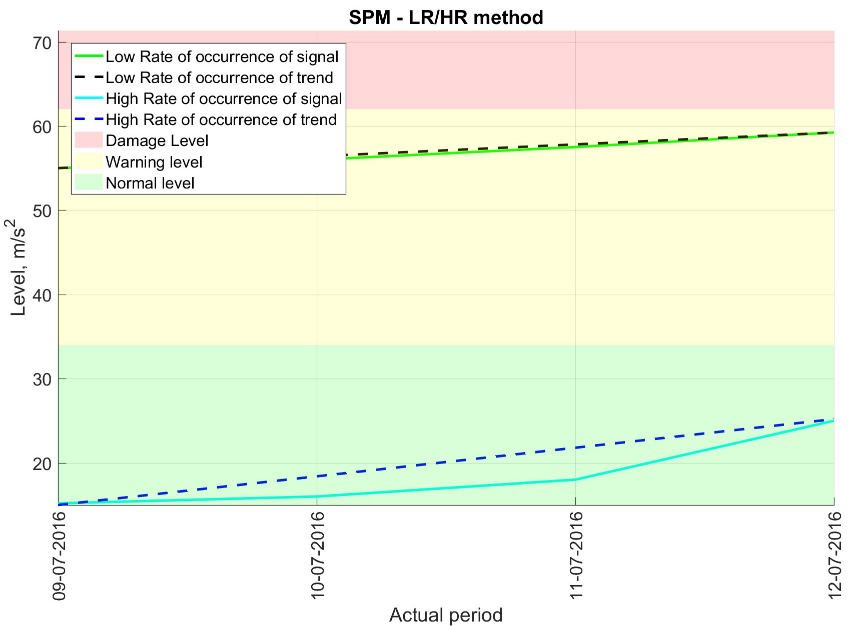
Для использования метода существует ограничение, связанное с конструктивным исполнением механизма. Поскольку необходимо исследовать высокочастотные колебательные процессы, которые сильно затухают на границах раздела материалов, для корректных измерений требуется, чтобы между наружным кольцом подшипника и местом установки датчика существовал сплошной массив металла.
Разработчики вибродиагностических методов каждый по-своему решали проблему нормирования этапов развития диагностируемых дефектов, но практическое представление примерно одинаково — это специальные таблицы или номограммы, предназначенные для практического использования группой экспертов.
Анализ метрических показателей сервисом VibroBox
VibroBox осуществляет анализ следующих одиночных и составных метрических показателей для виброускорения (виброскорости, виброперемещения):
- СКЗ — среднее квадратическое значение уровня анализируемого сигнала для выбранной полосы частот;
- ПИК — максимальное значение уровня сигнала для рассматриваемого интервала времени;
- ПИК-ФАКТОР — отношение параметра ПИК к СКЗ;
- ПИК-ПИК (размах) — разница между максимальным и минимальным уровнем сигнала для рассматриваемого интервала времени;
- коэффициент ЭКСЦЕССА (КУРТОЗИС) — мера остроты пика распределения случайной величины (мера дисперсии);
- значения косвенных параметров вибросигнала (рассчитанных с применением модифицированного командой VibroBox метода ударных импульсов SPM);
- 1/1-, 1/3-, 1/6-, 1/12-октавные спектры виброускорения;
- уровни вибрации в трех частотных диапазонах (согласно методикам стандартов серии ISO 15242-X);
- общий уровень вибрации (с применением методик, регламентируемых стандартами серии ISO 10816-X / ISO 20816-X);
- логарифмический уровень шума;
- скалограмма;
- др.
Для большинства метрических показателей алгоритмы анализа метрик VibroBox начинают свою работу с периода обучения, в течении которого происходит автоустановка пороговых значений. Полученные пороги в дальнейшем используются для формирования оповещений о достижении отдельными метрическими показателями опасных (предельных) уровней. C целью выявления динамики развития процессов, уменьшения вероятности ложной тревоги и повышения точности результатов анализа метрических показателей VibroBox проводит анализ развития метрических показателей с течением времени (Trend Analysis).
Пример 1/3-октавного спектра дефектного подшипника качения показан на рисунке 16.
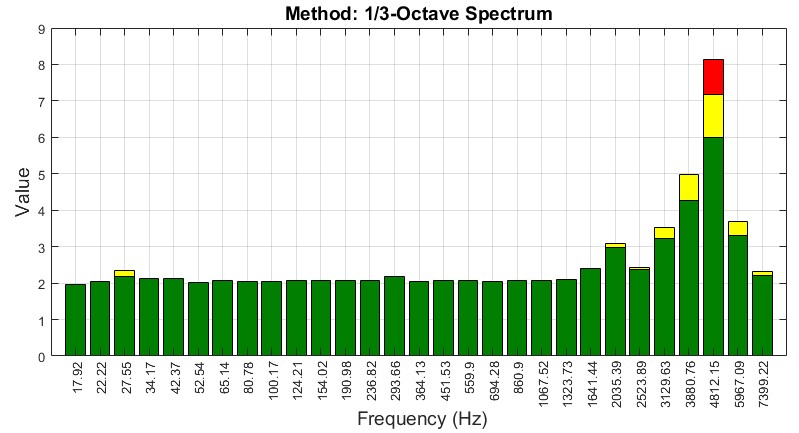
Анализ метрик не является достаточно информативным и достоверным для проведения глубокой диагностики оборудования, ввиду чего VibroBox реализует ряд дополнительных методов исследования вибрационных и телеметрических сигналов с использованием традиционных и авторских алгоритмов, описываемых далее.
6.5. Набор алгоритмов для оценки спектра сигнала и спектра огибающей вибрационного сигнала
Метод анализа спектральных компонент (анализ прямого спектра и спектра огибающей вибрационного сигнала) — наиболее популярный в настоящее время способ формирования пространства информативных признаков, в котором специалисты по вибродиагностике оценивают техническое состояние промышленного оборудования. Именно этот метод, впервые предложенный более пятидесяти лет назад, лежит сегодня в основе всех наиболее популярных систем вибродиагностики. Основные выражения этого метода — преобразование Фурье (2) и обратное преобразование Фурье (3):

Тем не менее, за более чем пятьдесят лет активной практики написано огромное количество учебников, разработаны и прописаны классификаторы (вибродиагностические карты) для большого количества разнообразного оборудования. Анализ этого, обусловленного многолетней прикладной практикой, опыта вносит свой вклад в развитие сервиса VibroBox.
Система VibroBox содержит блок расчёта спектра (спектральной плотности мощности) и спектра огибающей вибрационного сигнала, а ряд типовых вибродиагностических карт использованы для переобучения классификаторов. Все рассчитанные по спектру и спектру огибающей вибрационного сигнала информативные признаки участвуют в формировании общего вектора признаков технического состояния оборудования, по которому работает классификатор на основе нейронных сетей и нечёткой логики. Также VibroBox реализует анализ истории изменения характеристик (Trend Analysis) спектра вибрационного сигнала и спектра его огибающей с целью выявления динамики развития процессов.
Графическая интерпретация развития дефектов ременных передач и внутренних колец подшипников показана на рисунке 17.
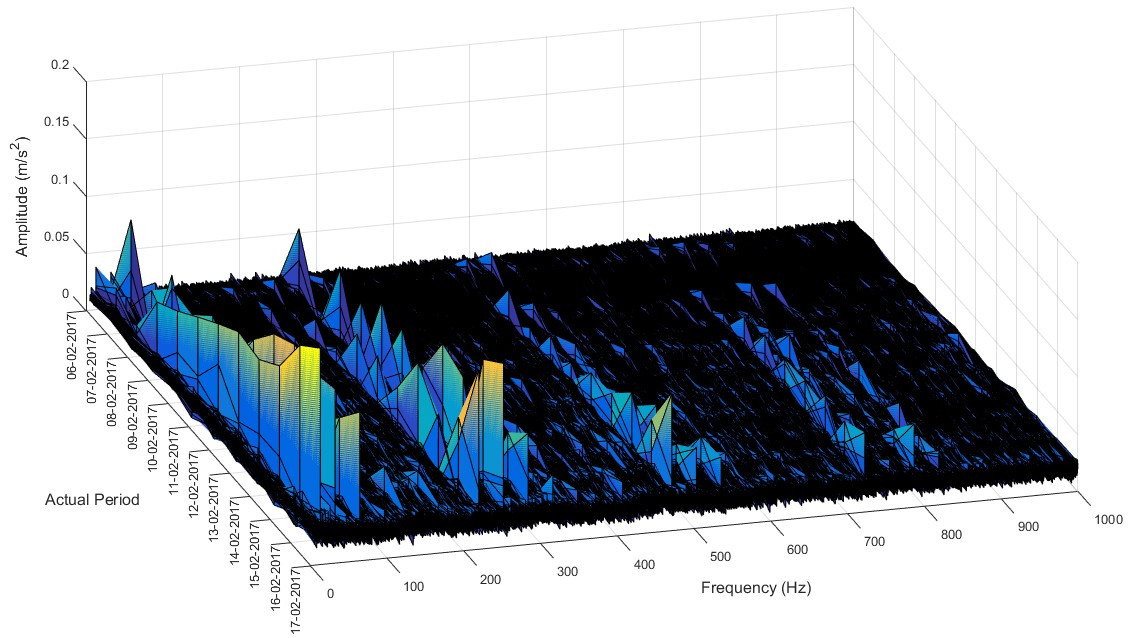
6.6. Набор алгоритмов для вейвлетной обработки вибрационного сигнала
Вейвлетный анализ (Wavelet Analysis) представляет собой особый тип линейного преобразования сигналов, предназначенный для их временнóй обработки (Waveform Analysis) и хорошо приспособленный для выявления кратковременных высокочастотных флуктуаций сигнала. Вейвлет-окно обеспечивает адекватную оценку таких флуктуаций за счёт увеличения амплитуды окна при уменьшении его ширины. Разрешающая способность анализа во временнóй области возрастает с ростом частоты.
Все эти особенности позволяет системе VibroBox эффективно применять вейвлетный анализ в задачах оценки технического состояния промышленного оборудования, так как именно наличие ударных периодических импульсов характерной формы, сопровождающих возникновение и развитие дефекта, является надёжным информативным признаком зарождения и развития дефектов.
Вейвлеты (wavelets — короткая волна) — функции определённой формы, локализованные по оси аргументов (независимых переменных), инвариантные к сдвигу и линейные к операции масштабирования (сжатия/растяжения). Они создаются с помощью специальных базисных функций, которые определяют их вид и свойства. По локализации во временнóм и частотном представлении вейвлеты занимают промежуточное положение между гармоническими (синусоидальными) функциями, локализованными по частоте, и функцией Дирака, локализованной во времени.
Вейвлет как функция ψ∈ L2(R) с нулевым средним:


Большинство дефектов роторного оборудования, имеющего в своём составе подшипники качения и зубчатые передачи, сопровождается ударными процессами с определёнными резонансными частотами. Вибрационный сигнал оборудования в зависимости от степени развития дефекта и их количества может содержать от одной до нескольких выраженных резонансных частот.
С точки зрения алгоритма вейвлетной декомпозиции вибрационный сигнал наиболее эффективно представлять не в виде суперпозиции большого количества сигнальных компонент, а ограничиться лишь имеющими наибольший энергетический вклад. Работа с каждой из этих компонент в отдельности позволяет упростить обработку. В спектральной области это возможно вследствие отсутствия эффекта «перекрытия шаблонов дефектов». Во временнóй области обработка упрощается вследствие того, что каждой реализации будет соответствовать одна периодическая (квазипериодическая) последовательность, что упрощает поиск периода повторения ударных импульсов.
Любой сигнал x(t) может быть представлен в виде суперпозиции определённых базисных функций. Разреженное представление такого сигнала имеет вид набора пиков. Каждый пик имеет базисную функцию φm, соответствующую трём параметрам: амплитуда, частота и позицией во времени. Математическое выражение этой модели сигнала с учётом аддитивного шума определяется выражением:

Амплитудный коэффициент sim и временнáя позиция τim определяются при помощи следующего выражения:

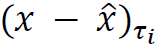
si — амплитуда базисной функции.
Точность восстановления сигнала будет зависеть от количества итераций выполнения алгоритма.
Первым этапом декомпозиции является вычисление скалограмм, по которым определяются резонансные частоты в декомпозируемом сигнале (см. рисунок 18). По выделенным точкам формируется узкий набор базисных функций (базис) и производится их нормирование (по энергии). На основании фрагмента сигнала вычисляется оптимальное количество итераций декомпозиции.
Сама декомпозиция представляет собой последовательную (итерационную) процедуру вычитания базисных функций из сигнала до достижения определённого уровня разложения. Фиксируя положение, амплитуду и масштаб вычитаемых функций, формируется разреженное представление сигнала (в виде набора импульсов для каждой базисной функции). На базе результатов разложения производится временнáя (поиск периодичностей, расчёт энергетического вклада и т.д.) и частотная (поиск шаблонов дефектов) обработки. Конечный вывод о состоянии оборудования делает модуль принятия решений.
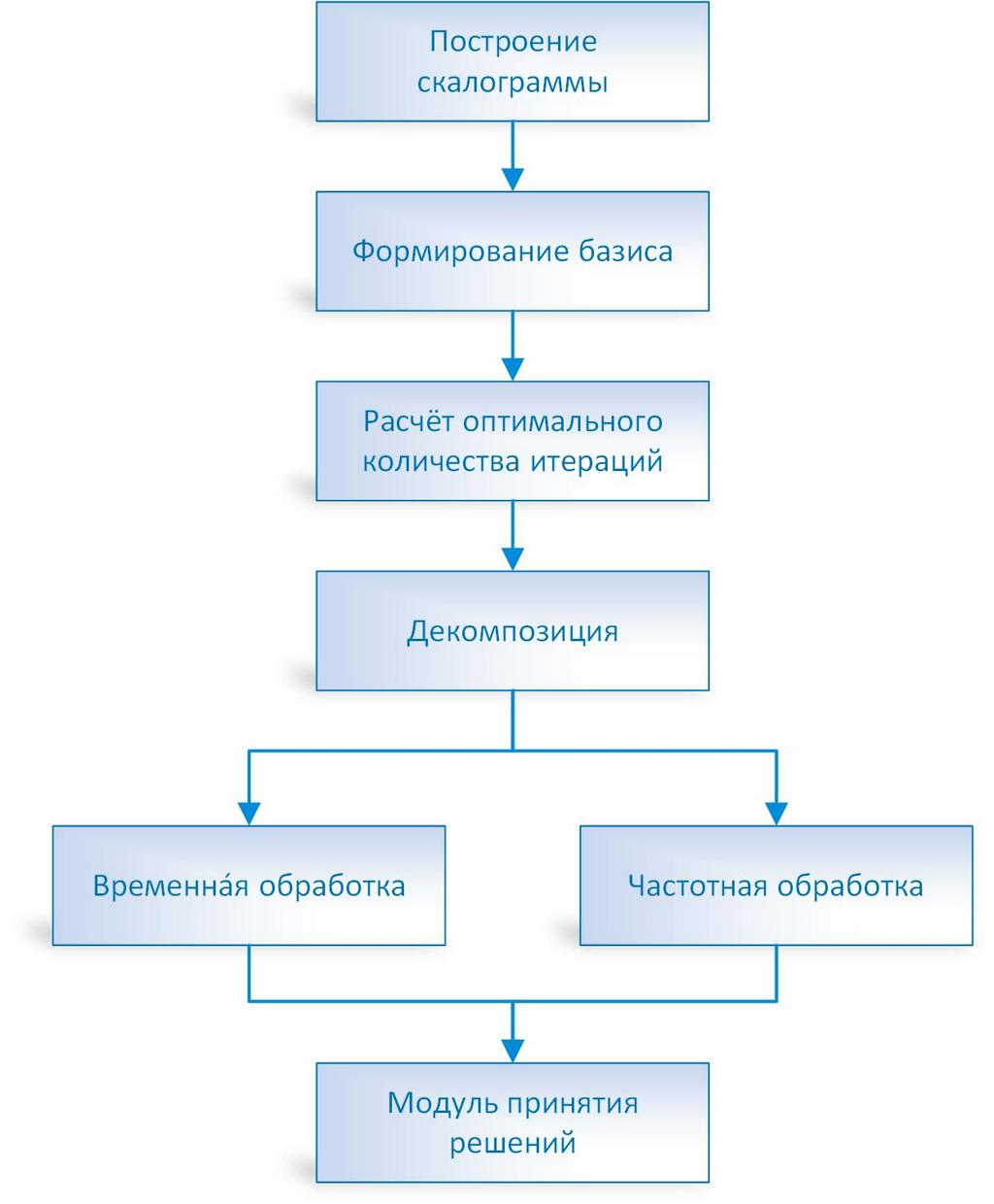
6.7. Базисная вейвлет-функция, адаптированная для выделения ударных импульсных процессов
Основа вейвлетного преобразования — базисная функция, форма которой во многом определяет эффективность метода для решения конкретной задачи. Вейвлетные базисы, в отличие от преобразования Фурье (Fourier transform), имеют достаточно много разнообразных базовых функций, свойства которых ориентированы на решение различных задач. Общим правилом при анализе сигналов является то, что вид базисной функции должен быть максимально подобен виду анализируемых данных.
Сигнал, возникающий от соударений элементов конструкции промышленного оборудования, имеет во временнóй области характерную форму — резко возникающего импульса с быстрым экспоненциальным затуханием. Частота затухающих колебаний определяется резонансными свойствами элементов конструкции. Поэтому базисная функция, адаптированная для обнаружения таких ударов, должна быть асимметрична, приспособлена для выделения характерного резкого скачка амплитуды колебаний в начале ударного импульса, должна иметь узкий Фурье-образ, т.е. содержать выраженную доминирующую частоту для обеспечения избирательности в частотной области. Закон убывания функции по возможности должен быть экспоненциальным.
Сервис VibroBox использует специально разработанные базисные вейвлетные функции для обнаружения ударных процессов в промышленном оборудовании. Эти функции являются предметом интеллектуальной собственности VibroBox.
![]() |
![]() |
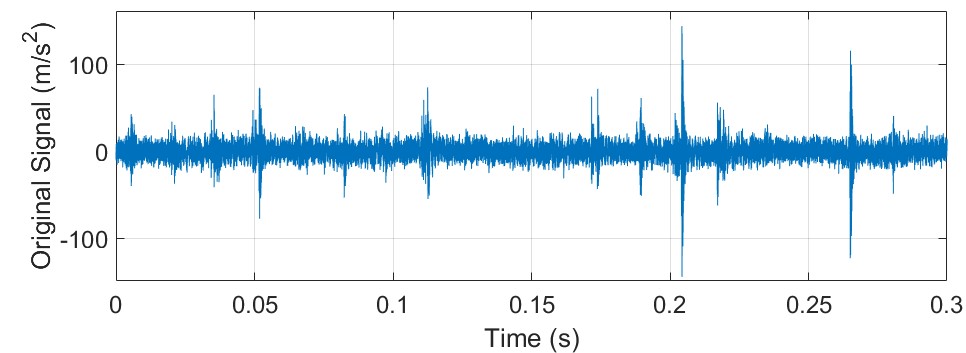
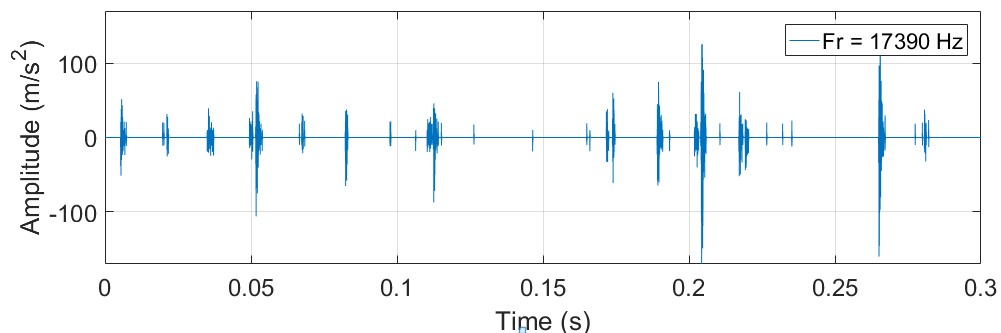
вейвлетной декомпозиции (SWD) с выделенными ударными импульсами,
имеющими резонансную частоту Fr=17 390 Гц (2-ая область на скалограмме).
Рисунок 19 — Пример осуществления разреженной вейвлетной декомпозиции.
6.8. Вектор информативных признаков технического состояния оборудования
Вектор информативных признаков технического состояния оборудования представляет собой наиболее полное описание вибрационного сигнала с точки зрения выявления возможных дефектов оборудования. В его формировании участвуют все наборы алгоритмов (методы), применяемые системой VibroBox для поиска признаков технического состояния оборудования.
В сформированном таким образом пространстве признаков работает классификатор на основе нейронных сетей и нечёткой логики, превращающий наборы признаков и их динамику в оценку состояния оборудования.
6.9. Классификация дефектов в пространстве информативных признаков
Задача классификации дефектов в пространстве информативных признаков — формирование оценки технического состояния оборудования на основе анализа вектора информативных признаков этого состояния.
6.10. Формирование предписаний по эксплуатации и обслуживанию оборудования
После того, как система классифицировала дефект оборудования либо выявила критическое несоответствие режимов его функционирования, необходимо назначить соответствующее этому состоянию предписание по техническому обслуживанию либо корректировке технологического процесса. Выявить проблему либо дефект и констатировать их наличие — недостаточно. Своевременно выявленная проблема лишь в совокупности с проведением корректирующих мероприятий позволяет купировать риски и существенно увеличить надёжность промышленного оборудования.
За эту задачу отвечает отдельная группа алгоритмов Vibrobox. Входные данные для их работы — оценка технического состояния оборудования.
6.11. Результаты работы сервиса VibroBox
Результатами работы сервиса являются оценка технического состояния оборудования, а также предписания по его эксплуатации и обслуживанию. Эти результаты отображаются в личном кабинете пользователя и могут быть автоматически предоставлены в системы управления предприятием (CMMS, MES, ERP) либо получены через программный интерфейс (API) любым другим сервисом.
Блок классификации дефектов
Блок классификации представляет собой предобученную нейронную сеть (Neural Network), работающую в пространстве признаков технического состояния оборудования.
Задача блока классификации — провести декомпозицию признаков и связать их с соответствующими состояниями оборудования.
Блок валидации дефектов
Блок валидации предназначен для поведенческой оценки связки признак-состояние во времени и снижения вероятности ложной тревоги. Работа блока валидации основана на технологии нечёткой логики и позволяет сервису проверять, насколько верны предположения классификатора о связках признак-состояние.
6.12. Перспективные алгоритмы
Кроме производственных технологий, решения назревших проблем ожидают и многие другие сферы, включая медицину, науку и различные онлайн-сервисы. До сих пор остаются нерешёнными задачи автоматизации принятия решений в областях, имеющих высокую вариативность объектов наблюдения — как технических, так и биологических. Важнейшую роль в решении данных задач играет формирование удобного пространства информативных признаков, которое позволит с минимальными рисками выполнять полностью автоматическую классификацию. Классические подходы базируются на предварительном анализе объектов наблюдения и формировании их детального описания посредством разработки схем, шаблонов, выставления пороговых уровней. А это неизбежно приводит к возникновению критических ошибок, вызванных ограниченным набором «обучающих» данных.
Поэтому мы стремимся создать универсальную систему принятия решений, функционирующую без априорной информации об анализируемом объекте. Наш подход подразумевает формирование адаптивного пространства информативных признаков, которое будет инвариантно к вариациям характеристик объектов наблюдения, и не подразумевает этапа предварительного обучения. Данное направление находится на стадии активной разработки, и уже получены результаты, указывающие на его перспективность не только для вибродиагностики (например, возможность восстанавливать подробную кинематическую схему оборудования из сигналов), но и для анализа временных сигналов другой природы (акустических, эхо-шумов сердца и т.д.).
Как мы это делаем?
Классификация массива «сырых данных» (сигналов вибрации, речи, шумов сердца) без предварительной обработки является неэффективной по многим причинам: зашумленность, непостоянство формы, зависимость от внешних условий, высокая размерность для прямой классификации и т.д. Поэтому для анализа временны́х сигналов и представления их в удобной форме, в основном, используются три области: временнáя, спектральная и спектрально-временнáя. Спектральная область хорошо изучена, обладает рядом инвариантных свойств и показывает прекрасные результаты при обработке стационарных сигналов (не изменяющих своих параметров во времени). Однако она не содержит информации о форме сигнала, которая во многих случаях имеет большое значение. Для работы с нестационарными сигналами было введено спектрально-временнóе представление. Однако форма сигнала в нём детально не анализируется. Речь идёт скорее об анализе распределения энергии по времени и частоте.
Поэтому форма сигнала может быть детально проанализирована только во временнóй области, не имеющей компактного и универсального (инвариантного) представления. Параметры, которые выделяются из неё современными системами (наборы простых метрик), не являются достаточными для достоверной классификации.
Представление формы временнóго сигнала в компактном, инвариантном виде позволяет упростить анализ в тех сферах, где её значимость высока (медицина, вибродиагностика, обработка речи и т.д.). Также это даёт возможность создать полное описание временнóго сигнала с позиции всех трёх областей: временнóй, спектральной и спектрально-временнóй. Всё это значительно улучшает качество работы нейронных сетей и делает их более универсальными.
7. Ближайшие планы
- Уже сегодня наша команда активно работает над устойчивым функционированием системы без предварительного указания типа диагностируемого оборудования и его кинематической схемы. Накопление необходимого количества данных телеметрии позволит решить задачу автоматического определения типа и создание математической модели («цифрового двойника») механизма по снятым вибрационным либо акустическим сигналам.
- Проводятся успешные эксперименты по анализу аудиосигнала и использованию широко распространённых смартфонов и планшетов в качестве простейшего инструмента для экспресс-диагностики.
- Мы работаем над интеграцией с высокоуровневыми платформами — SAP Cloud Platform for the Internet of Things, Predix, Intel IoT Platform.
- Мы активно исследуем не только промышленную, но и другие индустрии, где внедрение полностью автоматической системы диагностики и управления обслуживанием позволит уменьшить риски и принесёт явную выгоду.